Contents
Guide
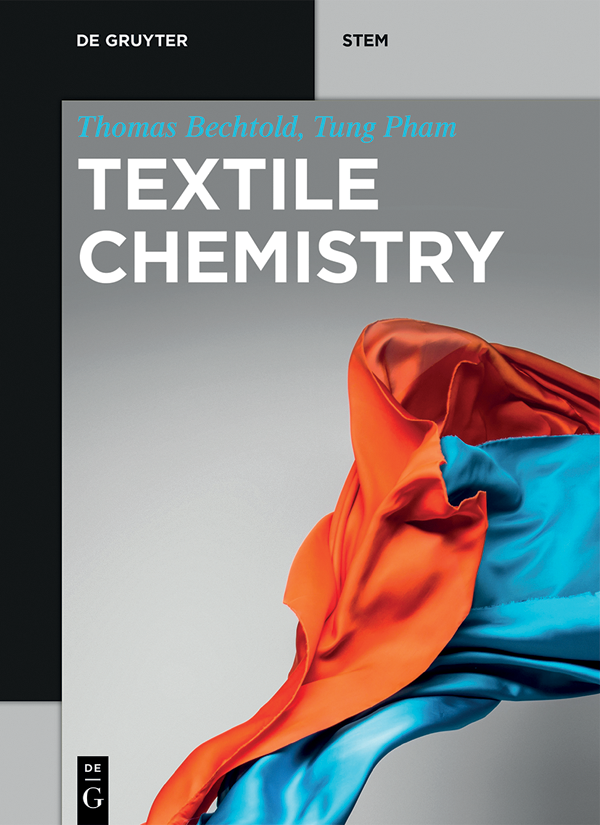
Thomas Bechtold, Tung Pham
Textile Chemistry
Also of interest
Inorganic Pigments.
Pfaff, 2017
ISBN 978-3-11-048450-2, e-ISBN 978-3-11-048451-9
Polymeric Surfactants.
Dispersion Stability and Industrial Applications
Tadros, 2017
ISBN 978-3-11-048722-0, e-ISBN 978-3-11-048728-2
Ionic Surfactants and Aqueous Solutions.
Biomolecules, Metals and Nanoparticles
Vera, Wilczek-Vera (Eds.), 2018
ISBN 978-3-11-056336-8, e-ISBN 978-3-11-056480-8
Textile Engineering.
An Introduction
Nawab (Ed.), 2016
ISBN 978-3-11-041324-3, e-ISBN 978-3-11-041326-7
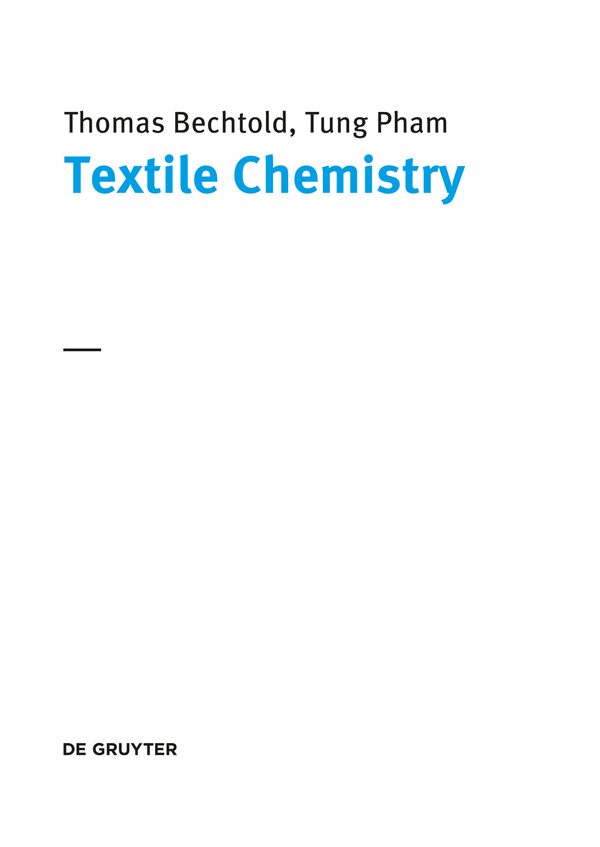
Authors
Prof. Dr. Thomas Bechtold
Research Institute for Textile Chemistry and Textile Physics
University of Innsbruck
Hoechsterstrasse 73
6950 Dornbirn
Austria
Prof. Dr. Tung Pham
Research Institute for Textile Chemistry and Textile Physics
University of Innsbruck
Hoechsterstrasse 73
6950 Dornbirn
Austria
ISBN 978-3-11-054984-3
e-ISBN (PDF) 978-3-11-054989-8
e-ISBN (EPUB) 978-3-11-054990-4
Library of Congress Control Number: 2018965042
Bibliographic information published by the Deutsche Nationalbibliothek
The Deutsche Nationalbibliothek lists this publication in the Deutsche Nationalbibliografie; detailed bibliographic data are available on the Internet at http://dnb.dnb.de.
2019 Walter de Gruyter GmbH, Berlin/Boston
Cover image: yurok / iStock / Getty Images Plus
www.degruyter.com
1 Textiles
1.1 Introduction
The architecture of a textile structure is a result of a combination of several production stages. The respective stage of production determines the principles of applicable textile chemical operations and also defines the final result. Application of some chemical treatment, for example, a colouration step, will lead to a completely different result when applied at the level of fibres or fabric.
This explains various properties and appearances of textile products, which also helps in continuous progress in the design of new products and exploring new properties. Examples of different levels of textile chemical modifications are summarised in .
Table 1.1: Relevant stages in textile processing, materials and processes, relevant characteristic properties and examples for products.
In various stages of textile processing and the materials are listed along the production chain. Each stage contributes to the development of characteristic properties, which are dependent on the choice of material, the combination of production steps and conditions.
Based on the stage where a textile chemical treatment is to be installed, the basic methodology and theoretical background as well as the technical equipment will differ.
With the rise of technical textiles, the scope of treatment and the field of applications for textile products have widened further. New techniques to obtain specialised properties, for example, electrical conductivity, surface modification by plasma or specific barrier properties through coating were introduced in textile chemical operations.
An almost endless number of variations and combinations of material and processing steps make a straight ordering and arrangement of textile chemical steps impossible; thus in this chapter, definitions of important textile technical terms and techniques are given to formulate a basic set of fundamental terms that will be useful for the other chapters.
1.2 Spinning
With the exception of silk, all other natural fibres that are of technical relevance are obtained in the form of staple fibres. Staple fibres exhibit a characteristic average length. In the spinning process, fibres are entangled, for example, by rotation, to increase the friction between the individual fibres and thus build a staple fibre yarn.
Different techniques are used to introduce the required number of turns per length into a spun yarn: ring spinning, open-end spinning, friction spinning and air-jet spinning. The characteristics of a yarn will depend on the spinning technology used. This will also influence the outcome of textile chemical operations as accessibility for chemicals will depend on the physical structure of a yarn (e.g., fineness of fibres, yarn count and number of turns per metre).
Synthetic fibres are fabricated as continuous filament fibres, namely, cables. The primary product of a fibre-spinning process is the endless fibre, the filament that, for example, has been obtained through melt extrusion. In rare cases, a single filament, the so-called monofilament, is the final product, which, for example, could be a string for a guitar or a fishing line. When several filaments are produced at the same spinneret, a multifilament is formed. A multifilament yarn, for example, is used to knit tights. For reasons of productivity, a very high number of holes are built in the same spinneret, which then result in a high number of filament yarns, forming a tow. The tow is then cut to staple fibres or is torn in a converter to deliver staple fibres.
Staple fibres are processed to yarns using similar procedure as that for natural fibres. At the stage of fibre spinning, fibre blends can also be formed; these blends are called intimate blends, for example, cotton/polyester (50/50) and cotton/polyamide (40/60).
When two or more yarns are wound together, a ply is formed. When different materials are wound together, another level of material blending is realised.
Corespun yarns consist of two material layers. The core forms the inner layer, for example, highly elastic polyurethane filament yarn, which then is wrapped with another material, for example, polyamide fibres, to cover the core material. In the given case, the core material is responsible for the high elasticity of the yarn, while the outer layer is required to achieve dyeability of the yarn.
1.3 Linear density yarn count
A characteristic measure to classify fibres and yarns is given by the linear density, which defines the mass of polymer per length of fibre or yarn []. Different systems for linear densities are in use; their use depends on the material and region.
Tex system (Tt): In the tex system, the mass of fibre, yarn in grams per 1,000 m length of fibre, yarn is considered ()). A yarn count of 1 tex corresponds to a mass of 1 g of material for a yarn length of 1,000 m. Thus in the tex system, the reference length l = 1,000 m. One kilometre of a yarn with 20 tex yarn count will exhibit a mass of 20 g.