Contents
Guide
Woven in Wire
DIMENSIONAL WIRE WEAVING IN FINE ART JEWELRY
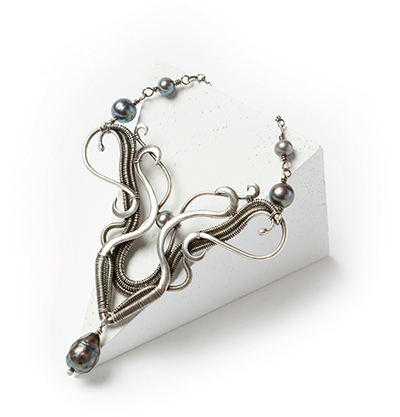
SARAH THOMPSON
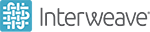
contents
introduction
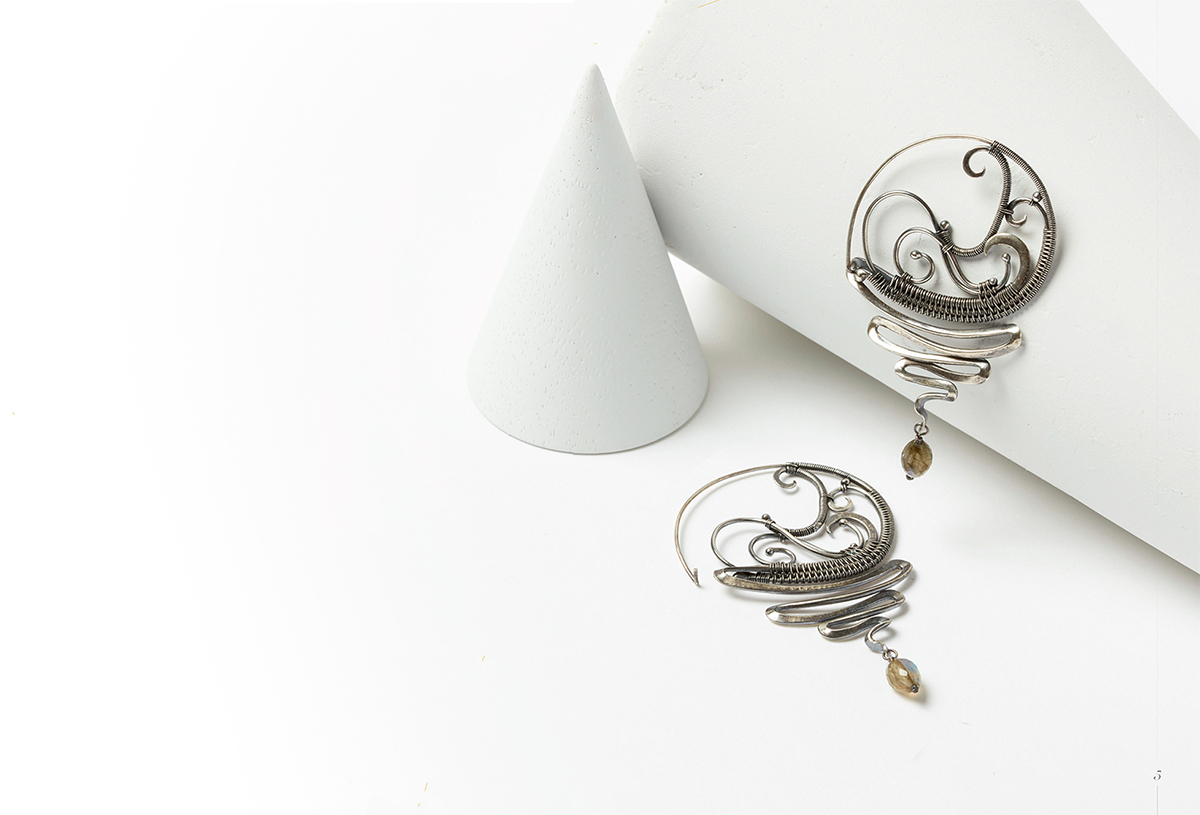
WHEN WRITING MY first book, I set out to teach and share with readers the technique at the heart of the jewelry I create, wire weaving with fine gauge wires. In Fine Art Wire Weaving I laid the groundwork for the solid foundation you and other jewelers need to successfully make pieces in my signature style. Now its time to take things to the next level with new inspiration, using techniques for sculptural effects and dimensional designs, and increasing the complexity of your work. Im setting out to challenge you, while providing guidance and support to grow your skills.
Im often asked how I make my master designs and what techniques I use to pull them together. The answers are here in the pages of this book. Im showing you everything from the tools and materials I prefer to the techniques I employ. Youll see each step of the process, but I will warn you, be prepared to invest time into the work well do together. Making the most of these techniques and achieving the level of beauty and intricacy of this style of jewelry requires patience. It isnt a skill mastered in an afternoonpractice is the key, and after all that practice you will be ready to transform your work into a masterpiece.
As we dig into the project chapters, well first explore Sculpting by applying sculptural techniques to wire weaving and using the moldable quality of wire to naturally enhance designs. With just a touch of dimension, Ill show you how to add life to your jewelry. From there we dive into Symmetry. By utilizing the symmetry techniques found in this book, Ill show you how to take your wirework to a professional level with truly sophisticated designs. In the final section, Transformation, well combine different design elements in creative ways that lead to breathtaking results.
Inspiration is found everywhere, and I hope by opening your eyes to how to layer more details, you will begin to find your own design path and have some real fun playing with wire.
CHAPTER ONE
tools
The tools needed to wire weave are basic. With your hands and pliers you're able to make a variety of beautiful projects. To take your work beyond the basics to introduce dimension, symmetry, and sculptural elements, you'll need more. In this chapter we'll explore all the tools used for the projects in this book. Having proper tools is important. It will dramatically reduce hand fatigue and improve the quality of your finished work.
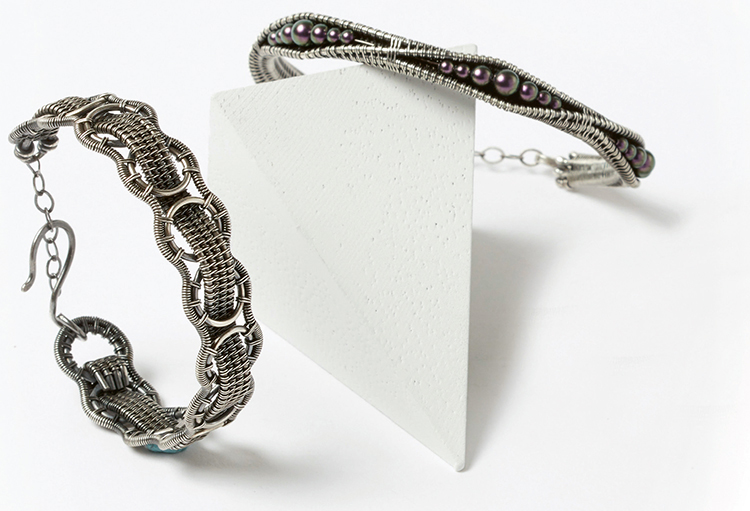
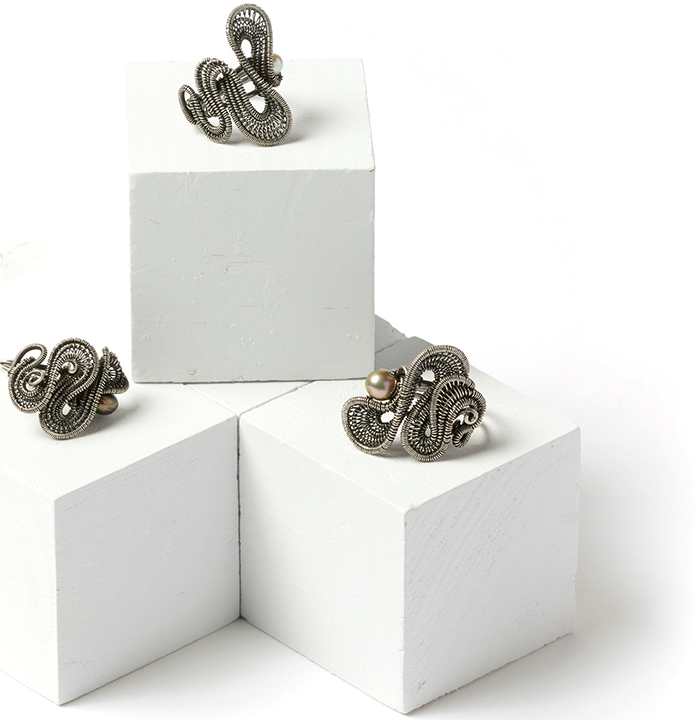
Forming Tools
Pliers and Cutters
Most of my wire shaping is done with three tools, and youll find these will quickly become your staples, too. Theyre common jewelry-making pliers and can be purchased anywhere from local bead stores to online specialty retailers. There are a few things you should look for when buying pliers, which I have noted here, but the best advice I can give is to purchase good quality tools. Youll have less hand fatigue thanks to the ergonomic design of higher-end pliers and your finished jewelry will have a more professional look.
CHAIN-NOSE AND FLAT-NOSE PLIERS are similar in that they both have flat inner jaws that youll use to grip your weaving and bend it into your desired shapes. I recommend using the version of these pliers that are smooth along the inner jaws and have a smaller inner nose. These will allow for more crisp angles. CHAIN-NOSE PLIERS taper to a narrow point that can get into small, tight spaces; FLAT-NOSE PLIERS taper to a thin, yet somewhat wide nose.
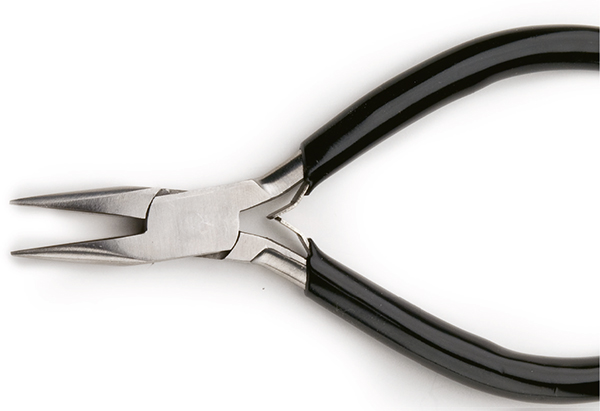
CHAIN-NOSE PLIERS
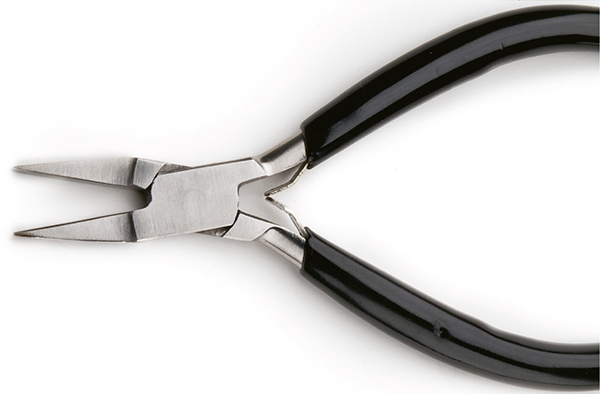
FLAT-NOSE PLIERS
The shafts of ROUND-NOSE PLIERS are cone shaped and should taper to a small diameter; the smaller the diameter, the tighter the loops you can make in your wire.
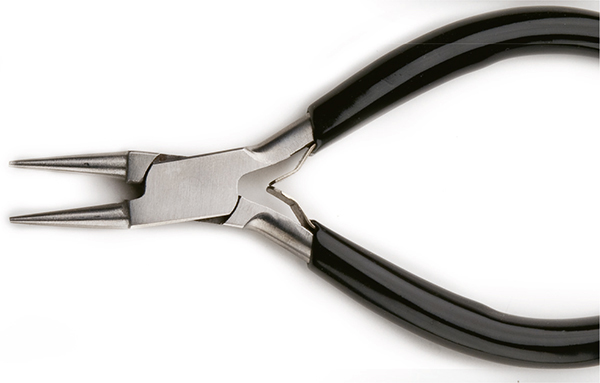
ROUND-NOSE PLIERS
NYLON-JAW PLIERS are often recommended for straightening and work hardening dead soft wire before working with it, but I prefer them for another purpose. I have found them very useful to manipulate and shape woven wires without marring the weave. I prefer the slim, flat-nose nylon-jaw pliers. Like the other pliers mentioned, the slim profile allows me to get into tight areas.
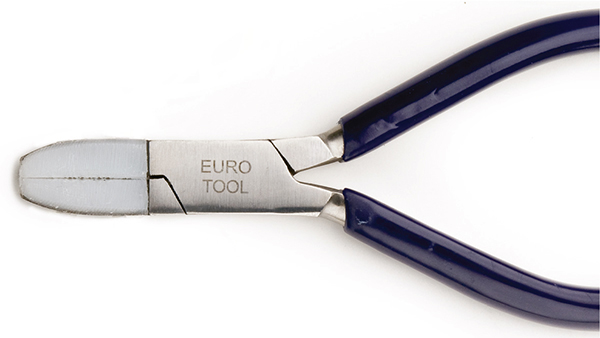
NYLON-JAW PLIRS
WIRE CUTTERS come in a variety of styles, but I prefer cutting wire with FLUSH CUTTERS . Their ability to make nice, clean cuts saves me time as I often dont need to file my wire ends. They are especially handy when I make my organic loops. Choosing a pair with a more pointed tip allows you to get into tighter areas to trim the wire as flush as possible. You will need your cutters to be able to cut up to 14-gauge wires.
Work Surface
The type of jewelry youll be making using my techniques requires a solid surface to work on. Youll be doing a lot of hammering, so something sturdy is a must. However, youll also have times when youre weaving large sections that call for a spot thats a bit more comfortable.
Youll need a STEEL BENCH BLOCK that is smooth and without dents for hammering and shaping wire. I prefer to use a bench block between 34" (7.510 cm) wide; this gives me enough work surface to hammer on. You can place a rubber mat, sandbag, or even a folded washcloth under the bench block to muffle the sound.
Hammers
A quality CHASING HAMMER is my go-to tool when flattening wire. Look for a hammer that has some weight to it, but not so heavy that it becomes uncomfortable or strains your wrist. It should feel comfortable when gripping the handle. The head should be smooth with no dents. If you can find a hammer with rounded edges, this will help prevent tool marks, especially if you are a beginner. Personally, I prefer Fretz hammers; they are comfortable when held and have the right amount of weight to them to ensure that my hammer is doing the work so that I can use less force when hammering.
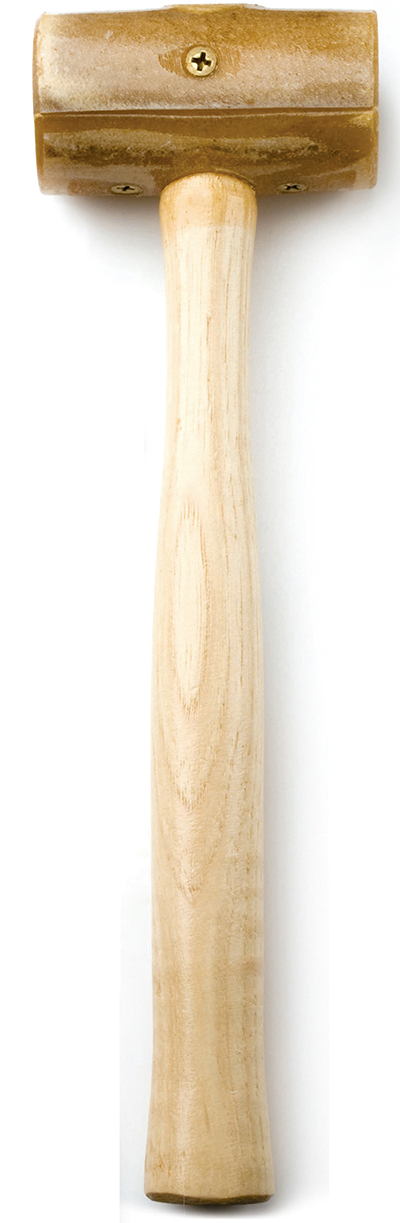
CHASING HAMMER
MALLETS are great to form the wire or woven strips around mandrels without marring them. Theyre available with rawhide, rubber, or silicone heads. My favorite mallet is the Bonny Doon 7oz. Urethane forming hammer. It forms woven strips beautifully around bracelet mandrels and doesnt leave a mark. My experience with other mallets shows you need to be careful how much force you use when forming, otherwise you can flatten the woven wire.