Wayne Goddard's
$50 Knife
Shop
REVISED
Get Started Without
Spending a Fortune
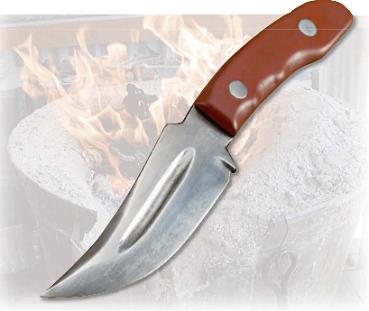
2006 Wayne Goddard
Published by
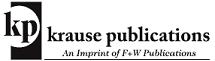
700 East State Steet Iola, WI 54990-0001
715-445-2214 888-457-2873
Our toll-free number to place an order or obtain
a free catalog is (800) 258-0929.
All rights reserved. No portion of this publication may be reproduced or transmitted in any form or by any means, electronic or mechanical, including photocopy, recording, or any information storage and retrieval system, without permission in writing from the publisher, except by a reviewer who may quote brief passages in a critical article or review to be printed in a magazine or newspaper, or electronically transmitted on radio, television, or the Internet.
Library of Congress Catalog Number: 2005906860
ISBN 10-digit: 0-89689-295-6
ISBN 13-digit: 978-0-89689-295-8
Designed by Kara Grundman
Edited by Kevin Michalowski
Printed in China
ACKNOWLEDGEMENTS
I thank God for giving me an inquisitive mind. I thank Phyllis for her love, devotion and support; she made my career as a knifemaker possible. I could not have done it working alone. It wouldnt have been possible for me to learn knifemaking and support my family at the same time. Phyllis worked so that we could pay the bills and have health insurance. She was a working partner in the knife business even though she wasnt in the shop with me. Thank you, Honey.
The pioneers of the modern handmade knife era made it easier for those of us who followed the trails they blazed. The knifemaker who had the most impact on my career was Bob Loveless. I was getting ready to go into knifemaking full time during 1971-1972 and Bob was never too busy to answer all my questions. I attended my first Knifemakers Guild show in 1972 and found Bob as supportive in person as he was over the phone and by mail. I appreciated his no nonsense and practical approach to knives and what they were about.
His purity of design and clean workmanship gave me a goal to strive for. Bob was always a leader in finding new and improved blade materials. A lot of the excitement and growth of the handmade knife world in those early years came from his introduction of 154-CM. Thanks, Bob.
Wayne Goddard
January 2006
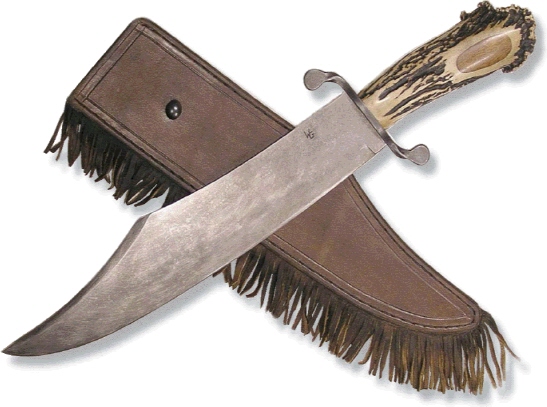
It takes practice and hard work, not fancy tools tomake a great-looking knife like this.
TABLE OF CONTENTS
INTRODUCTION
THE $50 KNIFE SHOP
B ack in 1988, I took on a project that was printed in Dixie Gun Works 1988 Blackpowder Annual. The plan was to make a forged buckskinner knife with a minimum of equipment. For that project, I built an anvil out of railroad rail, made a coal forge from a rusted-out barbecue and finished the knife by hand without the use of any power tools.
That project helped to spawn The $50 Knife Shop series for BLADEMagazine. The column was actually an expansion on my earlier experiments. It was a reaction to the high-tech methods that are being used to create hand-made knives today. Im not saying there is anything wrong with using technology and machine tools to their fullest extent. What I am saying is that high-tech it is not for everyone and this book is for those who want to simplify the process. Although the equipment is simple and low-cost, a high-quality knife can be made. It truly is possible to set up to both forge and grind knives and keep the budget under $50. The main requirement is having the desire to do it; I call it having the want-tos.
In the pages that follow I will be teaching my way through the two project knives that were finished in the magazine series. Along the way there will be some side trips to cover in-depth the things that there wasnt space for in the magazine series.
The Forged Project
The magazine series started out with forging because it requires a minimum of tools to get a finished knife. The Worlds Smallest Forge was used for forging the blade. The forged-to-shape blade was cleaned up with files and then hand-rubbed on wet-rocks made from broken sandstone grinding wheels to get it smooth enough for heat treatment. That was in keeping with the aim to use no power tools in the making of the forged blade. In order to keep the budget down; I used a tree branch from my dads yard for the handle.
The Stock-Removal Project
For this knife, I went back to 1963 and my start in knifemaking by constructing a faithful reproduction of my first grinder. It was made from a washing machine motor and some other junk. I used an abrasive saw on my reproduction grinder to cut a lawnmower blade into blanks. I then put a grinding wheel on it to shape the profile and grind the bevels. I used a disc sanding attachment on an electric drill to smooth it up and get it ready for heat treatment. I used a propane-torch to heat the one-brick forge. I used the goop quench to harden the two blades. Blades were tempered in a toaster oven. Scrap maple burl was used for the handle slabs on the stock-removal blade. Thats about as simple as it can get.
The Bottom Line
I started the magazine series with the assumption that I could make both the forged and stock-removal project for $50. I came in under budget, at least on paper. The following is a list of the materials and equipment that it took to complete the series.
Coal forge..$5
Makeshift anvil and forge tools$10
The Good News, Bad News Grinder$5
1955 Black and Decker Drill$2
Drill press adapterFree
Toaster oven..$2
Worlds Smallest Forge.$10
Blade and handle material for two knives$2
Total. $36
At the end of the series I made the comment that I should use the leftover $14 to build a belt grinder. I missed my estimate by $2; the final cost of the 1 by 42 belt grinder was built for $16 worth of yard sale parts. Youll find the details on it in the section on homemade grinders.
So then, we are about to undertake a couple projects that should teach you about knifemaking on a budget. The figure of $50 is really arbitrary. It is the philosophy of working with the tools you have or can acquire inexpensively thats really important. If you really want to, you can create a serviceable knife shop for a lot less than you think. 
CHAPTER 1
KNIFEMAKING SIMPLIFIED
T here is a well-known knifemaker who tells newcomers that an investment of $20,000 is necessary to fund a fully equipped shop. I cant disagree with that, however that shop will not make anyone a knifemaker. On the other hand, if a lot of tools were truly necessary, I and most of the makers who started in the 1960s and 1970s would never have made our first knives.
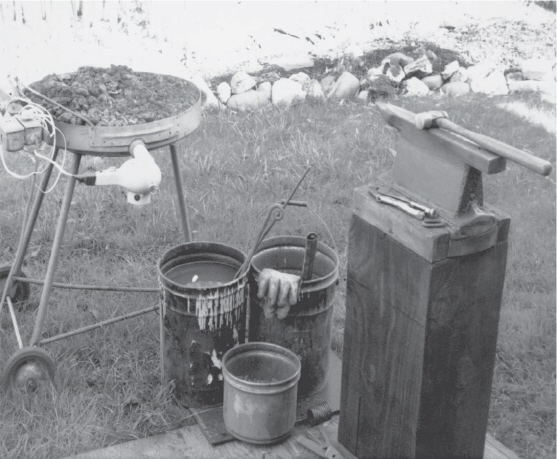
The backyard smithy, 1988.
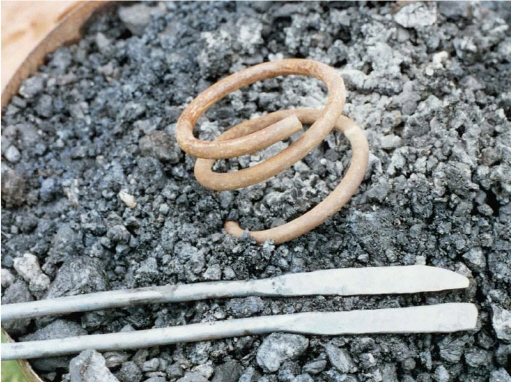
The coal forge made from a rusted out barbecue. A piece of Honda automobile spring, a flattened section on one piece, a pre-form on the other.
Next page