THE PEN TURNERS BIBLE
The Pen Turners Bible
The Art of Creating Custom Pens
Richard Kleinhenz
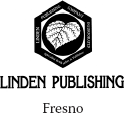
The Pen Turners Bible
The Art of Creating Custom Pens
by Richard Kleinhenz
All rights reserved. No part of this book may be reproduced or transmitted in any form or by any means, electronic or mechanical, including photocopying, recording, or by any information storage and retrieval system, without written permission from the publisher.
2012 Richard Kleinhenz
Cover design: James Goold
Design and layout: Maura J. Zimmer
Photography by Richard Kleinhenz except where noted.
Drawings Linden Publishing Inc.
ISBN 13: 978-1-610351-32-4
135798642
Linden Publishing titles may be purchased in quantity at special discounts for educational, business, or promotional use. To inquire about discount pricing, please refer to the contact information below. For permission to use any portion of this book for academic purposes, please contact the Copyright Clearance Center at www.copyright.com.
Woodworking is inherently dangerous. Your safety is your responsibility. Neither Linden Publishing nor the author assume any responsibility for any injuries or accidents.
Library of Congress Cataloging-in-Publication Data
Kleinhenz, Richard.
The pen turner's bible : the art of creating custom pens / Richard Kleinhenz.
p. cm.
Includes index.
ISBN 13: 978-1-610351-32-4 (pbk.)
1. Turning (Lathe work) 2. Pens. I. Title.
TT201.K59 2012
684'.083--dc23
2011038622
Linden Publishing Inc.
2006 S. Mary
Fresno, CA 93721
www.lindenpub.com
800-345-4447

Table of Contents

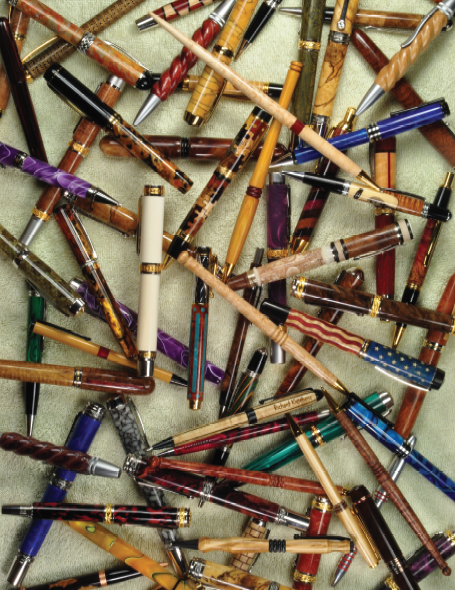
Introduction
I turn pens for enjoyment! Having been a hobby woodworker all of my life I discovered pen making in the mid nineties and never looked back. Making pens is my passion. Many wood turners consider pens an introductory project, a learning experience on their way to bigger and better things, but there are those that get absorbed in pensand I am one of them. I have also become involved with some Internet groups and have managed a group on Yahoo! for many years. I was a cofounder of the Penmakers Guild, another Yahoo! group that has attracted some of the finest pen makers I know. In recent years, we have made great strides to get pens recognized as more than a beginners project in woodturning craft circles.
Although I sell my pens through various venues, keeping my own cost low is not a primary consideration. I am not doing mass production, but working efficiently and with minimal waste of time and material is still important to me. I enjoy making some of my own tools and jigs, many of which are shared in this book.
Part of the appeal of pen making on a lathe is that a pen can be completed in one night. Even in this age of electronic communication, most of us still cant quite live without a non-electronic writing instrument, and a unique handcrafted pen adds pleasure to the use of such an old-fashioned device. As such, pens make wonderful gifts, and the craft of pen making in the home shop has grown by leaps and bounds in recent years. This in turn has taken the available hardware kits and components to levels we could only dream of in the 90s! A lot has happened since I first got involved with the craft: new styles, new materials, components with better plating, new techniques. In this book we use the latest pen kits, techniques and equipment and take the reader well past the basic kit into free design using a few purchased components. The book will introduce the reader to all of the basic techniques of making a pen on a wood lathe, with basic equipment. Some unique tools and jigs that rival or surpass commercially available tools are shown throughout the book. The first project covered in detail will get the reader to a completed modern pen that is more impressive than the slimline pen many people new to the craft tend to start out with, since those kits are most heavily marketed to the beginner. More advanced tools and techniques are introduced through over 20 pen projects, taking the reader all the way to advanced designs that make only minimal use of purchased components.
A chapter on common problems and their solutions is also included.
Inexpensive, imported metal lathes are available and open up a tremendous new area into which the pen maker can grow. We will use such a lathe not only to make our own tooling, but also to show the use of a metal lathe for most normal pen making operations. Well discuss design considerations for a kit-less pen made from resin and go though the construction step by step.
Finally, well feature work by some very talented pen makers, to stimulate more creative thoughts.
Section I:
The Basics
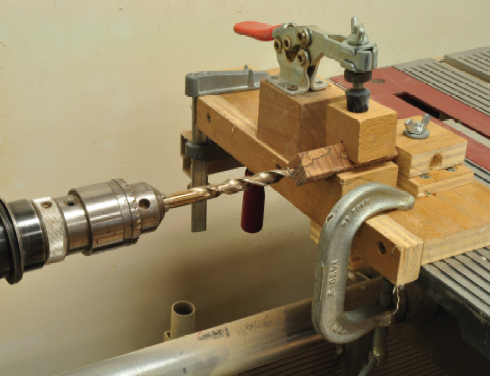
1. Basic Tools
The lathe
Shortly after we moved into our first (and current) house in 1983 I bought a Shopsmith Mark V. The tool paid for itself very quickly. I made some furniture and the display cases for eyeglasses my wife uses in her practice. Although I used all of the multi-purpose tools, I used the lathe least of all. I made a couple of childrens toys, but did not take a great liking to the lathe. In the mid 90s, at a woodworking show, I saw a gentleman from Penn State Industries turn pens. I was very taken with the result, but he used a tiny lathe, and I had a fairly large lathe at home. After watching for a while, we started talking, and when I told him I had a Shopsmith he said of course that lathe was suitablein fact they made a special mandrel for that very lathe! I walked away from their booth with a starter kit for the Shopsmith, went home and tried it. Indeed it worked! I used the Shopsmith for quite a few years as I advanced in the craft. Later I found that this starter package might not have been the best way to spend my money, but it got me going in a short time and I did not have to research the details of what I needed. The Internet was not as full of information back then as it is today! The main point is you can make pens on a large lathe, you dont need a mini-lathe.
Still, a mini-lathe is what I would recommend, if you dont already have a lathe in the family, or if you have a lathe along with a spouse who is unwilling to share it! A mini-lathe spins up faster, stops faster, and is often capable of higher speeds, which is an advantage for small-diameter turnings. For the same surface velocity, a small turning needs to turn much faster. You may make the final cuts on a small 6" bowl at 1000 RPM. To get the same surface speed on a " diameter pen the lathe would have to turn at 12000 RPM! There are some practical limits. Large lathes usually go up to 2000 or 2500 RPM, mini-lathes tend to go to 4000-5000 RPM. The main point is that spindle speed and turning diameter are related, and lathes are optimized for what they need to do. A suitable brand-new mini-lathe can often be had in the $200300 range.