FOUNDRY PRACTICE
A TREATISE ON
MOLDING AND CASTING
IN THEIR VARIOUS DETAILS
BY
JAMES M. TATE
AND
MELVIN O. STONE, M.E.
Copyright 2018 Read Books Ltd.
This book is copyright and may not be
reproduced or copied in any way without
the express permission of the publisher in writing
British Library Cataloguing-in-Publication Data
A catalogue record for this book is available from
the British Library
INTRODUCTION
IN administering the work in foundry practice at the University of Minnesota, the want of a good text-book has been a serious disadvantage. The work of the shop and that of the class-room should be correlatedshopwork should be studied and discussed in the class-room, and examples illustrating the various principles underlying good practice should be worked out in the shop.
While there have been some excellent books written upon the subject of foundry practice, yet, as a rule, these have been written with the needs of the experienced molder in view rather than those of the beginner. For this reason it is a difficult matter to teach the subject so that the student will acquire an intelligent understanding of its various details. The nomenclature and shop phraseology are not sufficiently elementary for the average beginner to grasp the statement presented, and much time is frequently spent in explaining an authors meaning.
The present little treatise has been written with a full knowledge of the problems involved and with the object of lessening some of the difficulties which arise in teaching the subject. The authors are both men of wide experience in foundry practice and its correlated subjects. Mr. Tate is an experienced pattern maker, who has been in charge of the pattern shop at the University of Minnesota for the past fifteen years, and during a part of this time he has also had charge of the work in the foundry. Mr. Stone is a graduate of the University, who has given especial attention to foundry work, both from the standpoint of the chemist and from that of the molder.
In presenting this work on foundry practice, the authors realize that it is not a complete treatise on the subject. The aim has been to produce a book in which the principles of foundry practice are set forth concisely and clearly. The needs of the engineering student rather than those of the practical foundryman were kept in view. To this end numerous examples are given representative of the different kinds of molding, and it is believed that the simple methods used in illustrating and describing the various operations involved and the reasons therefor will give the student a ready knowledge of the details of molding which will go far to supplement the practical work of the foundry, which, in a college course, must necessarily be limited.
While the treatment is thus somewhat brief, the subject matter as here presented is intended to cover all ordinary work in foundry practice, including both brass and iron casting.
A glossary of foundry terms has been added, as it has been found that to obtain the greatest value from a work of this character the reader must become familiar with names and expressions used by foundrymen, for even if it were possible to eliminate shop expressions, it would be undesirable to do so.
J. J. FLATHER,
Professor of Mechanical Engineering,
UNIVERSITY OF MINNESOTA
MINNEAPOLIS, MINNESOTA,
September, 1904.
CONTENTS
Plain mold. Parted pattern. Coping out. Bedding in. Setting cores. Check molding.
Dry sand mixtures. Venting. Drying, finishing, blacking. Skin-drying, pit mold, and sweeps.
Facing sand. Flasks. Gating. Gaggers. Soldiers. Nails and rods. Patching. Stopping off. Venting cores. Chaplets. Setting chaplets. Weighting and clamping. Shrink holes. Burning on, or casting on. Bench molding. Snap-flasks. A match. Molding machines.
Tapping hole. Tuyres. Charging door, hearth. Slag notch, lining, charging, tapping out. Ladles, blowers.
The chill. Mixture of iron for chilled casting.
The malleablizing process.
Hand work. Tumbling barrels, rattlers. Sand blast, pneumatic hammers, portable grinders.
Pneumatic crane. Hoist. Molding machine, chipping hammer. Sand rammer. Sifter.
The sand mixture. The mold. The mixtures of metal. Melting and converting.
Brass molding. The sand. The flask. The furnace. Oil furnaces.
FOUNDRY PRACTICE

CHAPTER I
GREEN SAND MOLDING
THE method of proceeding in making a mold for a plain casting may be demonstrated by consideration of the pattern shown in . The sand falling between these two rammings is then rammed to an even hardness sufficient to form a firm body and allow the free escape of the gases.
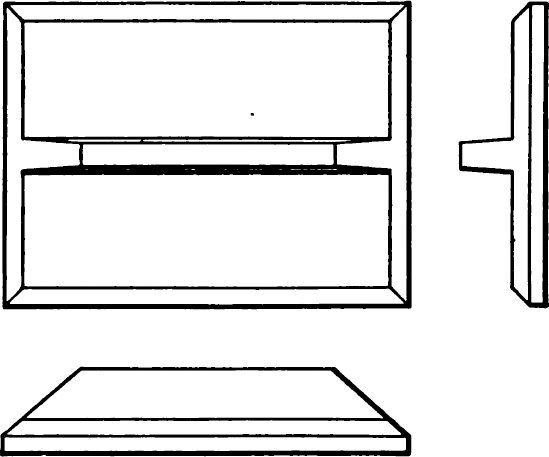
FIG. 1.

FIG. 2.
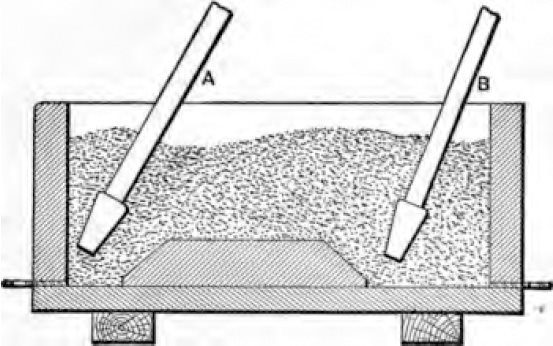
FIG. 3.
Care should be taken in ramming to avoid striking the rammer nearer to the pattern than one inch. Wherever the pein strikes the pattern, a hard spot is left in the sand which will cause a scab on the casting. The flask is now filled full of heap sand and rammed with the butt rammer, as shown in . The mold is now ready to cast.
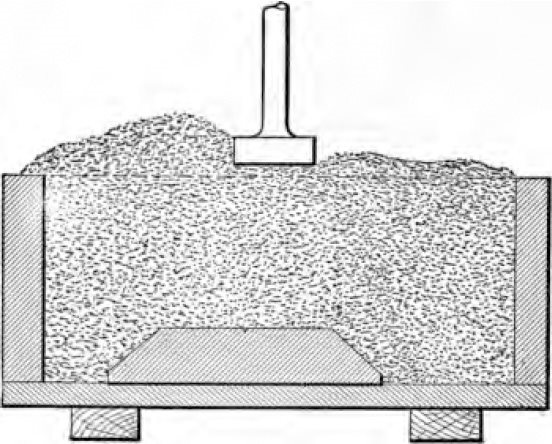
FIG. 4.
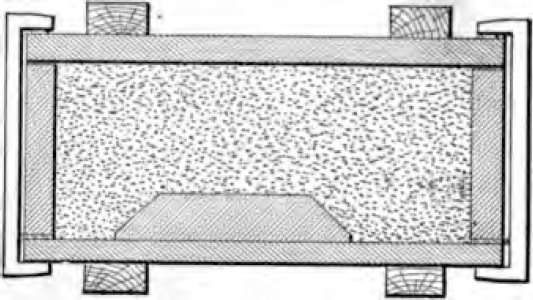
FIG. 5.
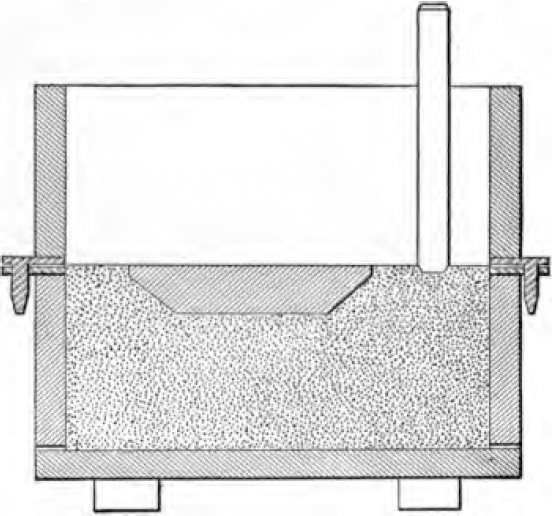
FIG. 6.
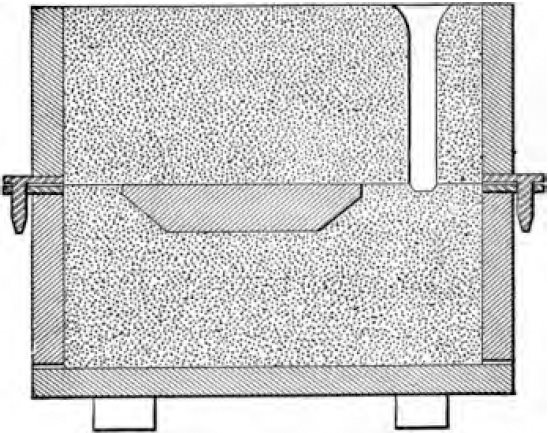
FIG. 7.
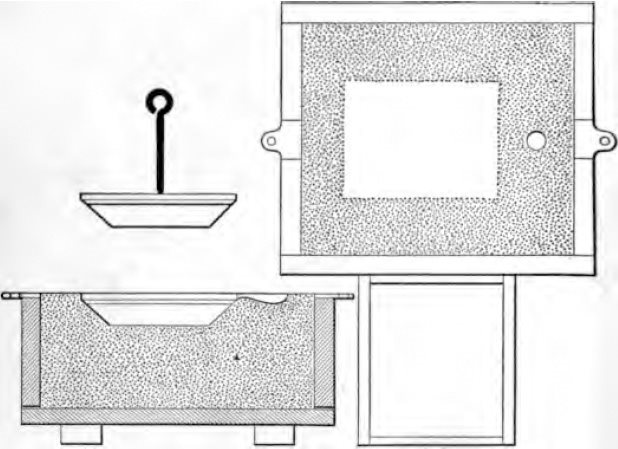
FIG. 8.
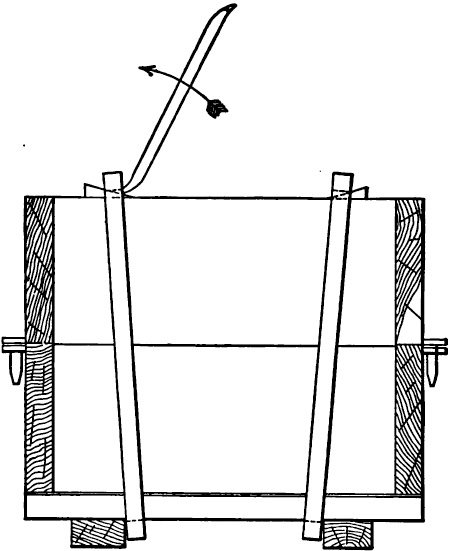
FIG. 9.
The process of making a mold with a split, or divided pattern is shown by the small pulley in .
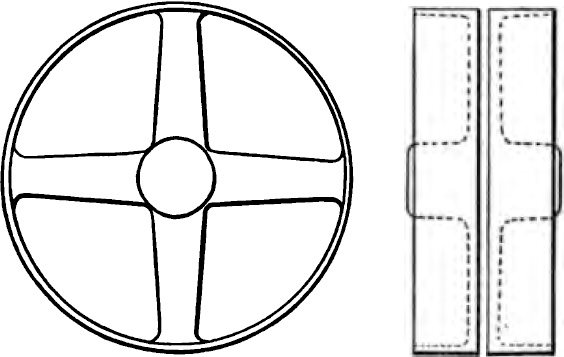
FIG. 10.
The pattern is now completely covered with riddled sand and the outside rammed as before. The sand within the pattern is rammed with any small tool or iron rod that can be gotten in between the soldiers and the pattern. The remainder of the drag is filled in, rammed and vented. The flask may now be turned over and the joint slicked as before. The other half of the pattern is put on as shown in . The pattern in the cope is brushed off and lightly swabbed with water.
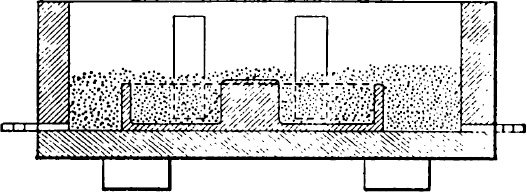