Dunbar - Woodturning Techniques - Furniture & Cabinetmaking
Here you can read online Dunbar - Woodturning Techniques - Furniture & Cabinetmaking full text of the book (entire story) in english for free. Download pdf and epub, get meaning, cover and reviews about this ebook. City: Cincinnati, year: 2017, publisher: F+W Media, genre: Romance novel. Description of the work, (preface) as well as reviews are available. Best literature library LitArk.com created for fans of good reading and offers a wide selection of genres:
Romance novel
Science fiction
Adventure
Detective
Science
History
Home and family
Prose
Art
Politics
Computer
Non-fiction
Religion
Business
Children
Humor
Choose a favorite category and find really read worthwhile books. Enjoy immersion in the world of imagination, feel the emotions of the characters or learn something new for yourself, make an fascinating discovery.
- Book:Woodturning Techniques - Furniture & Cabinetmaking
- Author:
- Publisher:F+W Media
- Genre:
- Year:2017
- City:Cincinnati
- Rating:4 / 5
- Favourites:Add to favourites
- Your mark:
- 80
- 1
- 2
- 3
- 4
- 5
Woodturning Techniques - Furniture & Cabinetmaking: summary, description and annotation
We offer to read an annotation, description, summary or preface (depends on what the author of the book "Woodturning Techniques - Furniture & Cabinetmaking" wrote himself). If you haven't found the necessary information about the book — write in the comments, we will try to find it.
Woodturning Techniques - Furniture & Cabinetmaking — read online for free the complete book (whole text) full work
Below is the text of the book, divided by pages. System saving the place of the last page read, allows you to conveniently read the book "Woodturning Techniques - Furniture & Cabinetmaking" online for free, without having to search again every time where you left off. Put a bookmark, and you can go to the page where you finished reading at any time.
Font size:
Interval:
Bookmark:
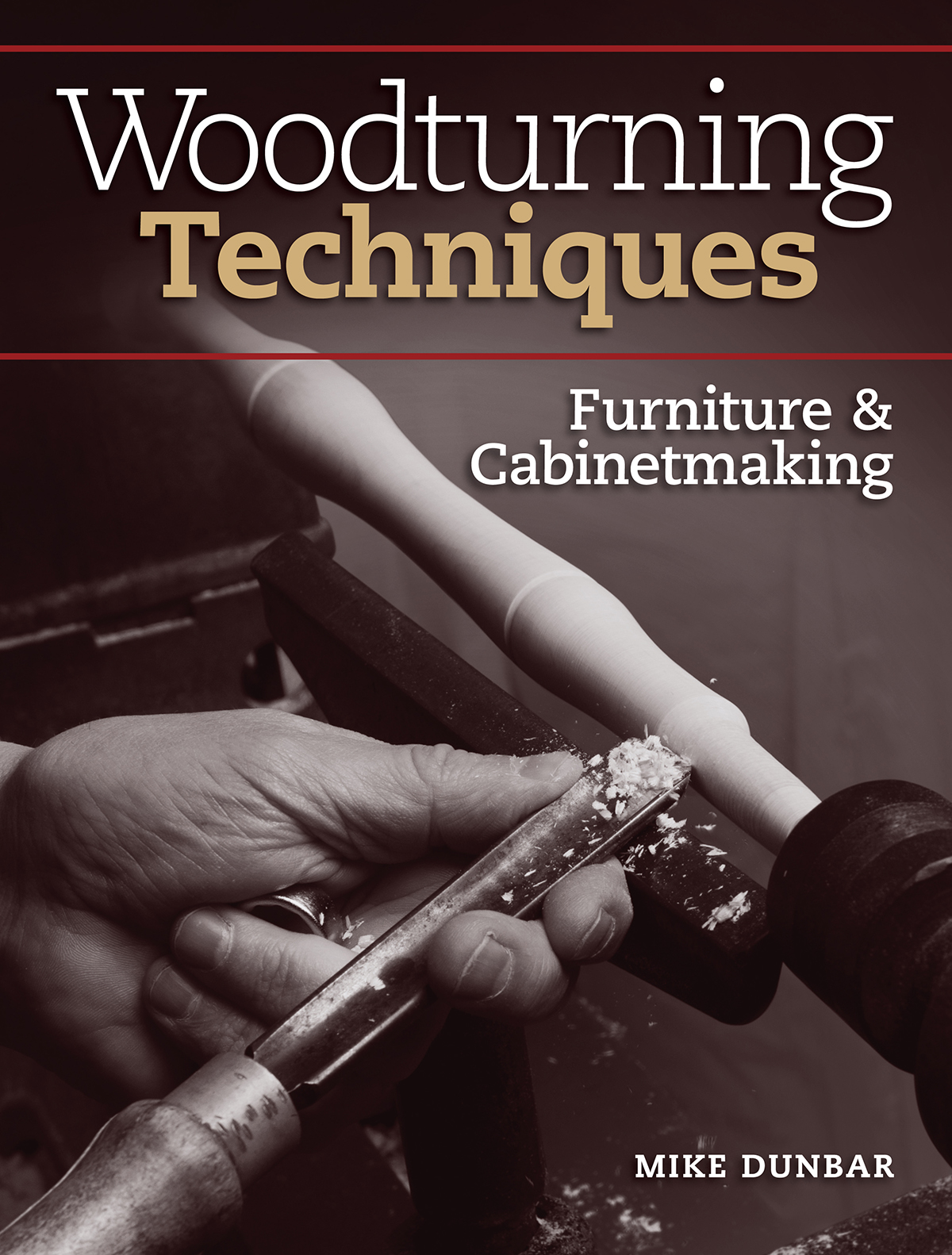
Techniques
CINCINNATI, OHIO
popularwoodworking.com
Sign up for our newsletter and receive special offers, access to free content, and information on the latest new releases and must-have woodworking resources! Plus, receive a free download for signing up.
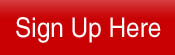
Visit us online to sign up at
http://www.popularwoodworking.com
The craft of working wood in a lathe is called turning. The people who do this work are called turners. Wood turning is an ancient craft that was practiced by most early civilizations. It was also a widespread craft. Most cultures produced large numbers of turners, and there was a great demand for their products.
Up until only several generations ago, turners in all western countries earned their living making the turned wooden products needed by the rest of society. Turners were considered an essential part of society, and were well-respected. Furthermore, these craftsmen were so accomplished that the term made in a lathe was used to describe anything that was cleverly and nicely executed.
Turning was different from many other woodworking trades in that turners did not usually make completed products. They did make some turned items that they sold directly to the consumer. These included such things as walking sticks, bowls, and other small utilitarian household goods that used to be called treenware, a corruption of the words tree ware. Most of the time, however, a turner made parts that were used by other woodworkers, principally furniture makers and builders.
There were reasons for this. Although turners were woodworkers, turning is a separate and distinct craft that demands particular skills and knowledge. In this way, it is very much like carving or marquetry. Carpenters, joiners, and cabinetmakers were all skilled craftsmen who needed turnings for their work, but they did not necessarily need to be able to turn.
There is another reason why turning was a distinct part of woodworking. Turning requires a large machine called a lathe. A lathe has always been an expensive piece of equipment. Furthermore, the lathe could not be easily disassembled and stored, so even when it was not being used, it still required its own space. Space has always been at a premium in crowded workshops. As a result, even though the woodworkers who built buildings or made furniture regularly used turnings in their work, they did not necessarily own a lathe, or know how to use one. They instead depended on turners.
Woodturners supplied the building trades with many products, including newel posts and balusters (the upright turnings under stair banisters), porch columns, roof balustrades, rosettes, corner blocks, and other architectural details. For furniture makers, turners produced the legs for chairs, tables, and case pieces, as well as bed posts, and even drawer pulls. Most of these parts are long and thin, and they were spindle-turned. Spindle turning is done with the wood secured between the lathes two centers.
After the mid 18th century, perhaps the largest consumer of turnings was the turned or common chair industry. Common chairs include Windsor, ladder-back, and Fancy (Hitchcock-type) chairs. These chairs were inexpensive, and were most often used in the kitchen. They are all still made today.
Traditionally, turners made few products that could be sold directly to customers. Most of those retail products were everyday utilitarian objects known as treenware, or sometimes just treen. The treenware shown here are a mortar and pestle, a hand mirror, a darning egg, a herb crusher, a spigot, a bowl, a rolling pin, and a set of clothespins.
While parts for formal (expensive) chairs were usually cut and shaped with saws and planes, the majority of the components in turned chairs were made in a lathe. Old chairmakers records dating from a time when most woodworking was still done by hand indicate that chairmakers purchased chair parts from turners in lots that had many thousands of pieces.
Besides doing predominantly spindle turning, old-time turners also made turnings that were used in sets. For example, they might make any of the following: a row of balusters, four table legs, the legs for a set of chairs, a pair of porch columns, or a set of drawer pulls. This indicates that besides knowing how to turn, a turner also knew how to duplicate the part make the same part over and over again.
Both the craft of woodturning and the turners who practice it have changed dramatically over the past couple of generations. Today, the building, furniture, and chair industries still consume large numbers of identical turned parts. However, the old skills are no longer necessary because spindle-turned parts are now made in factories on tracer and back knife lathes. The people who operate these machines, while still called turners, are really machine operators rather than highly skilled craftsmen. Their job now consists of knowing how to chuck up a wooden blank and how to turn on the machine. When the cutting is done, they turn off the lathe, remove the turning, and chuck up another piece. This job is a far cry from the skills once possessed by hand turners.
In spite of these mass-production turning factories, much of the lost handicraft of woodturning has been revived over the past few decades (as have many other branches of woodworking), and turning is now widely practiced by both professional and amateur turners alike. These modern craftspeople are very different from the machine operators who work in turning factories in that they are every bit as skilled as the old-time woodturners. In fact, in some ways they are even more talented.
However, during this revival, hand turning took on a new emphasis. Modern turners are more artistic than craft-oriented, and as artists they are more interested in giving expression through their understanding of wood than they are in making purely functional objects. In fact, many of their pieces are intended to be looked at and not used. As a result, modern turners no longer work as subcontractors providing their products to other crafts. Instead, they largely focus on making complete turned objects that stand alone, such as bowls, vases, and platters.
Modern turning also differs from old-time turning in that turners no longer make large numbers of the same object. In other words, they do not do a lot of duplication. Many of the objects made by todays turners are unique one-of-a-kind items. Although todays turners may work for a while on a certain design or type of turned object, they are usually exploring new ideas, not duplicating.
There is also another difference between old-time turning and modern turning. Old-time turned objects were inexpensive (for example, the turned parts for the turned chair industry). Most of the objects made by todays turners are very expensive, selling for prices that will make the uninitiated gasp with disbelief.
Font size:
Interval:
Bookmark:
Similar books «Woodturning Techniques - Furniture & Cabinetmaking»
Look at similar books to Woodturning Techniques - Furniture & Cabinetmaking. We have selected literature similar in name and meaning in the hope of providing readers with more options to find new, interesting, not yet read works.
Discussion, reviews of the book Woodturning Techniques - Furniture & Cabinetmaking and just readers' own opinions. Leave your comments, write what you think about the work, its meaning or the main characters. Specify what exactly you liked and what you didn't like, and why you think so.