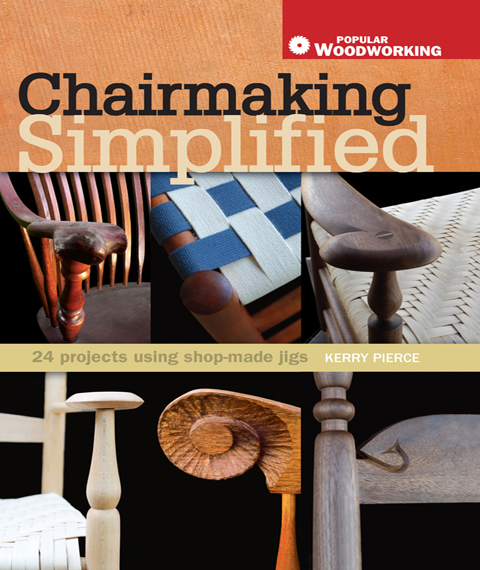
Chairmaking Simplified
KERRY PIERCE
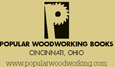
Chairmaking Simplified. Copyright 2008 by Kerry Pierce. All rights reserved. No part of this book may be reproduced in any form or by any electronic or mechanical means including information storage and retrieval systems without permission in writing from the publisher, except by a reviewer, who may quote brief passages in a review. Published by Popular Woodworking Books, an imprint of F+W Publications, Inc., 4700 East Galbraith Road, Cincinnati, Ohio, 45236. First edition.
Visit our Web site at www.popularwoodworking.com or our consumer Web site at www.fwbookstore.com for information on more resources for woodworkers and other arts and crafts projects.
Other fine Popular Woodworking Books are available from your local bookstore or direct from the publisher.
Library of Congress Cataloging-in-Publication Data Pierce, Kerry.
Pierce, Kerry.
Chairmaking simplified / by Kerry Pierce. 1st ed.
p. cm.
ISBN-13: 978-1-55870-827-3 (pbk. : alk. paper)
ISBN-13: 978-1-55870-959-1 (EPUB)
ISBN-10: 1-55870-827-8 (pbk. : alk. paper)
1. Chairs. 2. Woodwork. I. Title.
TS880.P525 2008
684.13 dc22
2007051181
Acquisitions Editor:
David Thiel
Senior Editor:
Jim Stack
Designer: Brian Roeth
Production Coordinator: Mark Griffin
Photographer: Lindsey Beckwith
Illustrator: Kevin Pierce

Metric Conversion Chart
to convert | to | multiply by |
---|
Inches | Centimeters | 2.54 |
Centimeters | Inches | 0.4 |
Feet | Centimeters | 30.5 |
Centimeters | Feet | 0.03 |
Yards | Meters | 0.9 |
Meters | Yards | 1.1 |
Read This Important Safety Notice
To prevent accidents, keep safety in mind while you work. Use the safety guards installed on power equipment; they are for your protection. When working on power equipment, keep fingers away from saw blades, wear safety goggles to prevent injuries from flying wood chips and sawdust, zear hearing protection and consider installing a dust vacuum to reduce the amount of airborne sawdust in your wood-shop. Don't wear loose clothing, such as neckties or shirts with loose sleeves, or jewelry, such as rings, necklaces or bracelets, when working on power equipment. Tie back long hair to prevent it from getting caught in your equipment. People who are sensitive to certain chemicals should check the chemical content of any product before using it. The authors and editors who compiled this book have tried to make the contents as accurate and correct as possible. Plans, illustrations, photographs and text have been carefully checked. All instructions, plans and projects should be carefully read, studied and understood before beginning construction. Due to the variability of local conditions, construction materials, skill levels, etc., neither the author nor Popular Woodworking Books assumes any responsibility for any accidents, injuries, damages or other losses incurred resulting from the material presented in this book. Prices listed for supplies and equipment were current at the time of publication and are subject to change.
About the Author
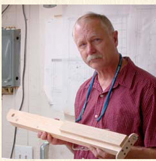
After earning a bachelor's degree in English from Bowling Green State University, and a master's degree in art from Ohio University, Kerry Pierce began a 30-year career as a professional furniture maker. He has specialized in Shaker and Shaker-inspired work for much of that career. Many of his 13 books and 80 magazine articles focus on Shaker woodworking. He has shown his Shaker-inspired work in a number of regional venues, most recently at Ohio Furniture by Contemporary Masters at the Decorative Arts Center of Ohio. He has served as Contributing Editor of Woodwork magazine since 1995, and is also a regular instructor at the Marc Adams School in Indianapolis, teaching most often about Shaker-style chair-making.
Dedication
For Sally, who taught me to read and to love books; for Jim, who taught me the pleasures of craftsmanship; for Elaine, Emily, and Andy, who have made my life complete; and for all the good people at Popular Woodworking Books, in particular Jim Stack and David Thiel.
And a special thanks to Sarah and the Larks.
I also want to acknowledge the assistance of the Warren County Historical Museum (wchmuseum.com) in Lebanon, Ohio, for allowing us access to their excellent Shaker furniture collection.
(The Mark Soukop profile ran originally in Woodwork magazine, and the Mike Herrel profile originally ran in Woodshop News.)
Preface
Let's face it, chairmaking can be intimidating. It's not really like any other branch of the woodworking tree. Who but a chairmaker knows how to use an inshave, an adze, or a side-rung-mortise jig? In fact, who but a chairmaker knows what these tools are? In addition, chair-making requires a working knowledge of technologies and skills foreign to most woodworkers. Who but a chairmaker regularly steams and bends wooden parts? Who but a chairmaker knows how to weave a seat from splint or Shaker tape or cattail leaves? In fact, who but a chairmaker knows cattail leaves are useful for anything at all?
Chairmaking can be intimidating, but it doesn't have to be, and that's what this book is all about. Its mission is to present simple and straightforward approaches to the chair-making craft, to make it possible for any woodworker with moderate skills to find success.
You will find more step-by-step photos here than in any other book on the subject. You will find clear, carefully-rendered measured drawings of a wider range of chairs than has ever before appeared in a single book from post-and-rung to Windsor, from Arts & Crafts to Appalachian country.
More important, in keeping with book's mission to simplify the chairmaking process, you will find on these pages jigs and fixtures that have never before appeared in any book. After almost 30 years as a chairmaker, a chairmaking instructor, and the author of three books and dozens of magazine articles on the subject of chairmaking, I decided to rethink the jig landscape, from the ground up, stripping it down so that you won't spend 40 hours building jigs to construct a chair that takes only 20 hours to build.
These methods and jigs are the result not only of my own experiences as a chairmaker; they are also the result of my years as a chairmaking instructor at the Marc Adams School, during which I was able to take a close look at the kinds of questions and problems that surfaced as the students in my classes built their first chairs.
In addition, Michael Herrel, a craftsman from Bexley, Ohio, shares his simplified method for Windsor chairmaking that includes some of the most ingenious shop-made chairmaking methods I've ever seen.
There are few workshop experiences as gratifying as building a chair. If you've ever wanted to try it but felt intimidated by what you've heard, turn the page. Step inside. I think you might find what you're looking for.
Next page