
Copyright 2012 by George Group. All rights reserved. Manufactured in the United States of America. Except as permitted under the United States Copyright Act of 1976, no part of this publication may be reproduced or distributed in any form or by any means, or stored in a database or retrieval system, without the prior written permission of the publisher.
ISBN: 978-0-07-179654-5
MHID: 0-07-179654-1
What Is Lean Six Sigma? 2004 by George Group
PRINT BOOK
ISBN: 978-0-07-142668-8
MHID: 0-07-142668-X
E-BOOK
ISBN: 978-0-07-149035-1
MHID: 0-07-149035-3
Lean Six Sigma Pocket Toolbook 2005 by George Group
PRINT BOOK
ISBN: 978-0-07-144119-3
MHID: 0-07-144119-0
This publication is designed to provide accurate and authoritative information in regard to the subject matter covered. It is sold with the understanding that neither the author nor the publisher is engaged in rendering legal, accounting, or other professional services. If legal advice or other expert assistance is required, the services of a competent professional person should be sought.
McGraw-Hill books are available at special quantity discounts to use as premiums and sales promotions, or for use in corporate training programs. To contact a representative, please e-mail us at bulksales@mcgraw-hill.com.
Contents
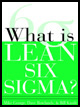
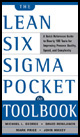
Acknowledgments
Thanks to the following people for providing support and input in developing this book: Jim Buckman, University of Minnesota; Dick Cunningham, Johns Manville; Mike Gabler, Solar Turbines; Linda Garner, The Plaquesmith; Todd Graham, Johns Manville; Gloria Grohs, Director of Nursing (ret.); Roger Hirt, City of Fort Wayne; George Maszle, Xerox Corporation; Ashish Merchant, Western Union; Dina Mongelli, Xerox Corporation; Heather Presley, City of Fort Wayne; Tim Schwalm, Eastman Kodak; Lynn Sherman, Delafoil Inc.; Barry Shook, Xerox Corporation; Tom Vandini, Delafoil Inc. Thanks also to Sue Reynard, our editor and layout staff all-in-one, and Tonya Schilling and Lynn Rae Kastle, our proofreaders.
CONTENTS
A Note to Our Readers
People who have been in business for some time will probably recognize Six Sigma as one of the most widely used quality improvement methods available today. Those in manufacturing may have heard about Lean, a discipline that focuses on process speed and efficiency. To many others, "Lean" may sound like a dieting technique, and "Six Sigma" will simply be a number and a Greek word, with no particular meaning.
Either way, you're probably reading this book because your company is starting a Lean Six Sigma initiative. This book provides answers to some of your most important questions: What is Lean Six Sigma? Why is my company using it? What can it do for me?
First things first. What is Lean Six Sigma? Some people call it an improvement method because it uses data to identify and eliminate process problems. Others call it an improvement engine because it establishes a whole new set of roles and procedures inside an organization that work to continuously generate results. As you'll see when you read this book, both are right. Lean Six Sigma lives within a broader framework of meeting a company's goals and customer needs.
What you'll find in What is Lean Six Sigma?
The purpose of this book is to introduce you to Lean Six Sigma. It focuses on key themes, and is not intended as a reference manual. It shows how Lean Six Sigma helps companies flourish in a new world where customers expect high quality and fast delivery at minimal cost.
The first six chapters of this book walk through the foundations of Lean Six Sigma. The chapters emphasize the basic vocabulary and concepts you'll likely start hearing in your own company.
The last chapters look at applications of Lean Six Sigma. We provide evidence showing why so many companies are turning to Lean Six Sigma, and present case studies from teams of people just like you who have used the concepts and methods to improve their workplace.
Introduction: What's In This For You
"There's money out there to be saved that you would not dream of when you start this," says Todd Graham. "That's the part I've really enjoyedsaving money for the plant."
Todd is an 18-year veteran of Johns Manville (JM), the only place he's worked since high school except for a brief stint as an auto mechanic. His career as a production/machine operator was going along smoothly until the late 1990s, when JM implemented what it called "variation reduction teams."
Though he had only a high school degree and a few college credits, Todd had always been interested in process improvement, so he applied to join a team and was accepted. Team members were pulled off their regular jobs, given some statistical training, and set to work. "Each variation reduction team made some progress," says Todd, "but they were really just a bunch of plant people struggling along. Nobody really knew what was going on in a broader sense."
That was about to change, however. In October 2001, Todd happened to see a JM newsletter that announced the company's intention to embark on something called Six Sigma. Todd recalls there weren't a lot of details given in the article, but it did mention the company was looking for people to volunteer to become something called "Black Belts," people who would be expected to manage projects at the plant locations. The article said that Black Belts would be required to commit at least two years to the job.
It sounded interesting to him, but Todd wasn't sure at first whether he wanted to get involved in the Six Sigma initiative. A month after seeing the notice, however, he was approached by management and asked to join the program, and he agreed. "What swayed me to become a Black Belt was the support I saw from the main headquarters," says Todd. "I thought that would mean we'd get much more support than we got on the variation reduction teams." As it turned out, he was right. "Top-down support has been really good," he says.
Soon after, Todd was officially relieved of his regular job responsibilities as he embarked on the first of five weeks of training. "The first week was all about leadership," he explains. "Then we did four weeks of additional training, spaced about a month apart. We'd get a week of training, then go back into the plant to work on a project, come back for more training, return to the project, and so on."
Todd describes his work on the training project as a real eye opening experience. "We didn't realize it would be so difficult to get useful data," says Todd. In the process he was studying, a number of raw products are melted together to make glass. The team's goal was to make the process and product more consistent, so they wanted to measure how well the materials were blended before and after transport. "It could take two or three weeks to get the samples analyzed," Todd says. "That meant that data I was looking at on any given day reflected what was happening three weeks ago. That didn't help me manage what's going on now."
Ultimately, he says, the team was able to solve only some of the data issues. They reached perhaps 40% of the original goal for the project. "What I learned is that projects have to be scoped properly," he adds. To that end, JM's insulation division recently brought together all of its Black Belts for a two-day course on project selection and screening.
Next page