Contents
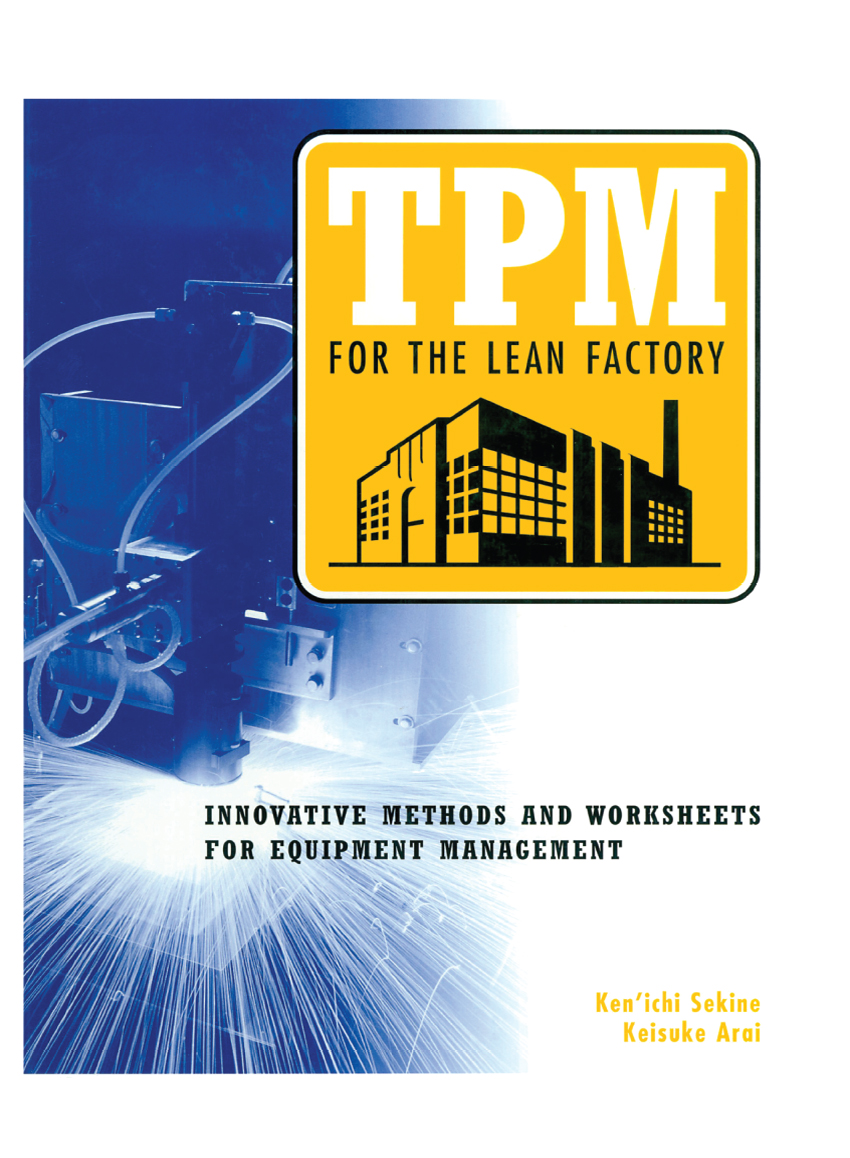
TPM for the Lean Factory
INNOVATIVE METHODS AND WORKSHEETS FOR EQUIPMENT MANAGEMENT
TPM for the Lean Factory
INNOVATIVE METHODS AND WORKSHEETS FOR EQUIPMENT MANAGEMENT
Kenichi Sekine
Keisuke Arai

Originally published as Kakushin TPM Manuaru. 1992 and 1998 by Kenichi Sekine and Keisuke Arai. Published by Techno Publishing, Tokyo, Japan.
English edition 1998 by Productivity, Inc.
Translated by Karen Sandness.
All rights reserved. No part of this book may be reproduced or utilized in any form or by any means, electronic or mechanical, including photocopying, recording, or by any information storage and retrieval system, without permission in writing from the publisher.
Additional copies of this book are available from the publisher. Discounts are available for multiple copies through the Productivity Press Sales Department (800-394-6868). Address all other inquiries to:
Productivity Press
P.O. Box 13390
Portland, OR 97213-0390
United States of America
Telephone: 503-235-0600
Telefax: 503-235-0909
E-mail:
Cover design by Mark Weinstein
Page, figure, and table composition by William H. Brunson, Typography Services
Additional figures by Lee Smith, Smith & Fredrick Graphics
Illustrations by Gordon Ekdahl, Fineline Graphics
Printed and bound by BookCrafters in the United States of America
Library of Congress Cataloging-in-Publication Data
Sekine, Kenichi, 1926
[Kakushin TPM manyuaru. English]
TPM for the lean factory : innovative methods and worksheets for equipment management / Kenichi Sekine, Keisuke Arai.
p. cm.
Translation of: Kakushin TPM manyuaru.
Includes bibliographical references and index.
ISBN 1-56327-191-5 (hc.)
1. Total productive maintenance. I. Arai, Keisuke. II. Title.
TS192.S4513 1998
658.202dc21
98-36058
CIP
03 02 01 00 99 98 10 9 8 7 6 5 4 3 2
Contents
Lean manufacturing cannot happen in a factory that lacks dependable, effective equipment. When equipment has a history of breakdowns and defective operation, a plant must maintain excess work-in-process and finished inventory just in case When minor stoppages eat into productive time, employees have to watch automated equipment that should run by itself.
Ideally, total productive maintenance (TPM) provides a framework for addressing these problems. During factory visits over the years, however, lean manufacturing experts Kenichi Sekine and Keisuke Arai have seen many companies that fail to reap the full benefit from their TPM activities. Sekine and Arai are careful observers of factory dynamics, and they have recognized the key equipment-related problems and misunderstandings that cause plants to miss their lean manufacturing goals. TPM for the Lean Factory shares their results-oriented TPM Innovation methods with a wider Western audience.
This book will be most useful to readers who have some experience with implementing the basic pillars of a TPM program, such as autonomous maintenance to inspect equipment and maintain operating conditions, or focused improvement to reduce equipment-related losses. The authors unique TPM Innovation approach refocuses the purpose of such activities, using a Toyota Production System-style emphasis on elimination of waste. introduces seven wastes that stem, in their view, from incomplete implementation of TPM. To eradicate these wastes, Sekine and Arai emphasize three main topics in the first six chapters: the new 5Ss, instant maintenance, and improved setup operations.
5S refers to a set of activities designed to improve the safety and functionality of the workplace itself; it is a critical first step in any improvement program. In , the authors describe a new approach to 5S to replace superficial campaigns that stop at posters, slogans, and cosmetic cleanup. The new 5Ss draw on workplace discipline as a foundation, but emphasize the first two Ss: Organization and Orderliness. These two principles promote standard locations for needed items and standard labels that help everyone find and store things properly. When implemented properly, the authors believe, the other three Ss Cleanliness, Standardized Cleanup, and Disciplinevirtually take care of themselves. An example from Mynac, a garment assembly factory, highlights some of the features of their approach.
page_xiiThe instant maintenance approach outlined in is a system for making quick repairs of small failures, such as broken limit switches. It also includes suggestions for preventive modifications and standardization of repair methods so everyone can respond quickly. Although the idea of standardizing your breakdown maintenance routines may seem counter to the preventive and life-extending focus of TPM, the authors are really suggesting that we be prepared for the unexpected, like emergency medical technicians for machines. Unexpected failures can happen, and its helpful to plan in advance how to fix them quickly.
Improving setup operations is a forte of Sekine and Arai, who give an extended presentation of their methods in Kaizen for Quick Changeover (Productivity Press, 1992). In of this book, they focus on organizing the preparation area for setup in a U-shaped line for efficient gathering and storage of the appropriate materials and tools. This approach saves time and helps avoid errors that could cause breakdowns or defects.
deals with planned downtime: the losses that come from inefficiently planned lines and underutilized equipment. This productivity loss falls outside the major equipment losses traditionally measured by overall equipment effectiveness (OEE), but it is especially significant from the larger lean manufacturing perspective of avoiding waste. The fix is not equipment improvement per se, but rethinking product families for efficient use of existing equipment.
Product defects are a form of waste no factory can afford to ignore. Defects often result from major or minor equipment failures, but the causes are often elusive and multifaceted. outlines a method for identifying important defect and failure factors using testing methods such as orthogonal arrays.
offers a wealth of resources on making daily equipment inspections more effective. The authors share steps for teaching employees how to conduct inspections and for managing spare parts. General steps are given for eliminating minor stoppages, and a set of checklists helps operators use their senses (sight, hearing, touch, and smell) to spot future trouble at its early stages.
presents a set of test yourself questions and answers, similar to questions that appear in earlier chapters. You will notice that these questions dont always review the books material; they are more in the nature of extra credit questions drawing on the readers own background knowledge. The questions throw light on the breadth and depth of knowledge that is expected of manufacturing managers in Japan.
The topics in Chapters 1 through 9 are summarized in an implementation overview that sets out in condensed, flowchart form the basic steps for implementing each topic. The overview topics are keyed to a set of 50 worksheet examples and blanks that support implementation. We hope you will use these as models to build forms that meet the specific needs of your workplace.
Kenichi Sekine and Keisuke Arai are among the leading lean manufacturing consultants in Japan. In addition to this book and