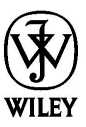




Contents
Preface
The paradigm of manufacturing is undergoing a major evolution throughout the world. The use of computers and the Internet has changed the way that we engineer and manufacture products. According to recent trends in manufacturing, products are subjected to a shorter product life, frequent design changes, small lot sizes, and small in-process inventory restrictions.
Computer-aided design (CAD) and computer-aided manufacturing (CAM) have become the standard for designing and manufacturing sophisticated products. Today we use CAD systems routinely to design products, and we produce them on flexible or programmable manufacturing systems (CAM). Managing manufacturing systems effectively has become as critical as using the proper engineering technology to process engineered components. Reducing waste for all aspects of engineering and production has become critical for businesses' survivability.
Improving Production with Lean Thinking is a departure from traditional production books. This book is intended for use in a course that traditionally has been titled, "Production Control," "Operations Management," "Manufacturing Systems," or "Production Management," and it is intended to provide a comprehensive view of issues related to this area, with a specific focus on lean engineering principles. This book is full of practical production examples of how lean thinking can be applied effectively to production systems.
Ever since Henry Ford pioneered manufacturing transfer flow systems and Fredrick Taylor wrote of scientific management, the world began to change by bringing high-tech consumer products into the lives of the common person. Our ability to manufacture quality products economically has inflated the standard of living throughout the world. Back in the beginning of the industrial revolution, Henry Ford doubled his worker's wages while cutting the cost of his automobile in half. This changed society forever by increasing wealth and making products more affordable. Today we have seen the same reductions in the cost of electronics hardware come about from applying good engineering and management science practice. In our global society, it is as important as ever that we use the most efficient production methods possible.
For almost a century, the United States was the world leader in automobile production. Today, however, the Toyota production system is viewed as the model for production efficiency. Interestingly, the developer of this philosophy, Taiichi Ohno, acknowledges that the stimulus for his system was his close reading of Ford's ideas. Because of this rediscovery, a new vocabulary based primarily on Japanese words to describe some of Ford's principles has found its way into all the world's manufacturing systems. Words such as kanban, kaizen, and jidoka are used routinely to describe approaches to reduce waste and make production more efficient. Mr. Ohno, Mr. Shingo, and other Japanese engineers developed a systematic approach to implement some of the good production practices that go back to the beginning of the 1900s. However, it has become far more important to systematize lean thinking because the complexity of products has increased and product life continues to get smaller and smaller.
Engineered products touch our lives everyday. Our ability to produce quality products economically affects our very standard of living. A constant focus of this book is on a systematic approach to improving production activities using lean manufacturing techniques. We feel strongly that successful managers and engineers of the future will need to understand and apply these techniques in their daily work activities. It is this area that we highlight in this book.
Unlike other production control books, this book attempts to provide a strong practical focus, along with the science and analytical background for manufacturing, improving, control, and design. This book is an excellent professional reference and also is an excellent text for instruction in both engineering and business schools.
This book comes with a companion Instructor's Manual that includes presentations as well as tests and examples.
Creating this book has proved that production challenges today are similar worldwide. Javier Santos and Jose Manuel Torres work at the University of Navarra (Spain), and Richard Wysk is professor at The Pennsylvania State University (USA). Therefore, this book includes European and American approaches to lean manufacturing issues.
This book marks the end of countless hours spent by the authors trying to refine a traditional topic into one that "hooks" to other engineering science activities. Several of our colleagues and outside reviewers read the manuscript and provided invaluable suggestions and contributions. Among them are Dr. Sanjay Joshi at The Pennsylvania State University, Dr. Matthew Frank at Iowa State University, and Bertan Altuntas. Special thanks are also due to Pablo Callejo for his artwork throughout this book. Finally, we would like to thank our families for tolerating us during the difficult parts of our writing.
Javier Santos
Richard A. Wysk
Jose Manuel Torres
1
Continuous Improvement
Tools
Asian culture has had a significant impact on the rest of the world. Other cultures have learned and adopted many words frequently used in our daily languages related to martial arts, religion, or food.
Within the business environment, Japan has contributed greatly to the language of business with numerous concepts that represent continuous improvement tools (kaizen tools) and with production philosophies such as just-in-time. Just-in-time (JIT) philosophy is also known as lean manufacturing. In this first chapter, both of these production philosophies will be discussed.
Another important philosophy that will be studied in this book is the concept developed by a Japanese consultant named Kobayashi. This concept is based on a methodology of 20 keys leading business on a course of continuous improvement (kaizen). These 20 keys also will be presented in this chapter.
Finally, in this introductory chapter the production core elements will be presented in order to focus on improvement actions. In addition, a resource rate to measure improvement results is also explained.