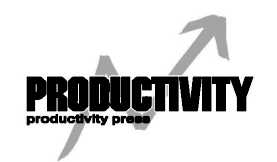




Dedication
Thanks to my dad and Debi, whose constant love and support have carried me through these years and allowed me to chase my dream. And, thanks to my great clients who have worked with us to implement fundamental new thoughts and actions.
-Beau Keyte
To Eileen, without your love and support I could never succeed. Thanks to all of the companies with whom I have workedyou are the true innovators.
-Drew Locher
To everyone at the Lean Enterprise Institute and the Lean Enterprise Academy for giving us the opportunity, time and support in testing these new waters. Special thanks to John Shook and Mike Rother for paving the way.
Whenever there is a product for a customer, there is a value stream. The challenge lies in seeing it.
-Mike Rother and John Shook, Learning to See
When you have learned to see value streams in individual facilities, it's time to see and then optimize entire value streams from raw material to the customer.
-Dan Jones and Jim Womak, Seeing the Whole
When you have learned to see the "raw material to the customer" value stream, it's time to see, challenge, and optimize how the rest of the enterprise supports the core value stream.
-Beau Keyte and Drew Locher
Contents
Foreword ix
Introduction xi
Chapter 1: Applying Value Stream Mapping to Information Management 1
Applying Value Stream Mapping to Non-production Areas 3
Purpose of the Case Study 4
Chapter 2: Getting Started: Mapping Office Value Streams 5
Understanding Value Stream Mapping Basics 6
Scoping the Selected Value Stream and Choosing the Mapping Team 8
Chapter 3: Identifying Office Wastes 15
Determining Value from Waste in Administrative Activities 16
Chapter 4: ABC Design's Lean Transformation in the Production Area 19
Chapter 5: Assessing the Office Current State 23
Step 1: Document Customer Information and Need 24
Step 2: Identify Main Processes (In Order) 24
Step 3: Select Process Metrics 25
Step 4: Perform Value Stream Walk Through 33
Step 5: Establish How Each Process Prioritizes Work 33
Step 6: Calculate System Summary Metrics 34
Chapter 6: Designing the Current State Map for ABC Design 37
Step 1: Documenting Customer Information and Need 38
Step 2: Identifying Main Processes (In Order) 39
Steps 3 and 4: Selecting Process Metrics and Filling In the Data Boxes 40
Step 5: Establishing How Each Process Prioritizes Work 46
Step 6: Calculating System Summary Metrics 47
Reflecting on the Current State Map 50
Chapter 7: Thinking Lean at the Functional Level 55
Sales, Marketing, and Operations 56
Order Processing 57
New Product Design 59
Inventory Control 60
Purchasing and Inventory Management 61
Scheduling and Production Control 62
Quality Management 63
Cost Accounting 64
General Accounting 65
Human Resources 66
Chapter 8: Designing a Future State 67
Question 1: What Does the Customer Really Need? 68
Question 2: How Often Will Performance Be Checked? 70
Question 3: Which Steps Create Value and Which Generate Waste? 72
Question 4: How Can Work Flow with Fewer Interruptions? 73
Question 5: How Will Work Be Controlled Between Interruptions? 76
Question 6: How Will the Workload And/Or Activities be Balanced? 78
Question 7: What Process Improvements Will Be Necessary to Achieve the Future State? 79
Chapter 9: Designing ABC's Future State 81
Assessing Customer Requirements 81
Determining Management Time Frame 83
Removing Wastes 84
Flowing Work 88
Pulling Work 93
Leveling Work 94
Achieving ABC's Future State 94
Summing Up-Results of ABC's First Future State 95
Chapter 10: Achieving the Future State 97
Tie the Value Stream Design to the Company's Business Objectives 97
Break the Work Plan into Loops 98
Prioritize Loop Implementation 98
Create a Work Plan and Cross-Functional Implementation Teams 103
Enabling Value Stream Management 104
Appendix 107
About the Authors
F oreword
An alternate title for this book could be Waste in the Office: The Final Lean Frontier. Beau Keyte and Drew Locher have accomplished an ambitious taskone that can benefit anyone concerned with creating maximum value for customers with as little waste as possible.
How much waste is there in an enterprise? Stated differently, what percent of activities undertaken by each of us every day actually contribute toward the creation of value for our customers? Quantifying waste on such a scale would, no doubt, be an endeavor that would in itself constitute waste, and a massive amount of it at that. Certainly, when we ask how many of our actions directly provide value for our customers, the answer is loud and clear: painfully little.
Since the publications of The Machine That Changed the World in 1989 and Lean Thinking in 1997, hundreds if not thousands of firms around the world have launched initiatives to eliminate waste in their operations. Many of those efforts have been fantastically successful while others have proved frustratingly slow or even ineffective. Either way, the great majority of those efforts have been aimed at the plant floor or other direct operations. Yet, as firms proceed with improvement activities on the plant floor they encounter the inevitable reality that fundamental change-even on the plant floorultimately requires the involvement and support of the entire enterprise.