Ed Barr - Sheet Metal Shaping
Here you can read online Ed Barr - Sheet Metal Shaping full text of the book (entire story) in english for free. Download pdf and epub, get meaning, cover and reviews about this ebook. year: 2019, publisher: Motorbooks, genre: Home and family. Description of the work, (preface) as well as reviews are available. Best literature library LitArk.com created for fans of good reading and offers a wide selection of genres:
Romance novel
Science fiction
Adventure
Detective
Science
History
Home and family
Prose
Art
Politics
Computer
Non-fiction
Religion
Business
Children
Humor
Choose a favorite category and find really read worthwhile books. Enjoy immersion in the world of imagination, feel the emotions of the characters or learn something new for yourself, make an fascinating discovery.

- Book:Sheet Metal Shaping
- Author:
- Publisher:Motorbooks
- Genre:
- Year:2019
- Rating:3 / 5
- Favourites:Add to favourites
- Your mark:
- 60
- 1
- 2
- 3
- 4
- 5
Sheet Metal Shaping: summary, description and annotation
We offer to read an annotation, description, summary or preface (depends on what the author of the book "Sheet Metal Shaping" wrote himself). If you haven't found the necessary information about the book — write in the comments, we will try to find it.
Sheet Metal Shaping — read online for free the complete book (whole text) full work
Below is the text of the book, divided by pages. System saving the place of the last page read, allows you to conveniently read the book "Sheet Metal Shaping" online for free, without having to search again every time where you left off. Put a bookmark, and you can go to the page where you finished reading at any time.
Font size:
Interval:
Bookmark:
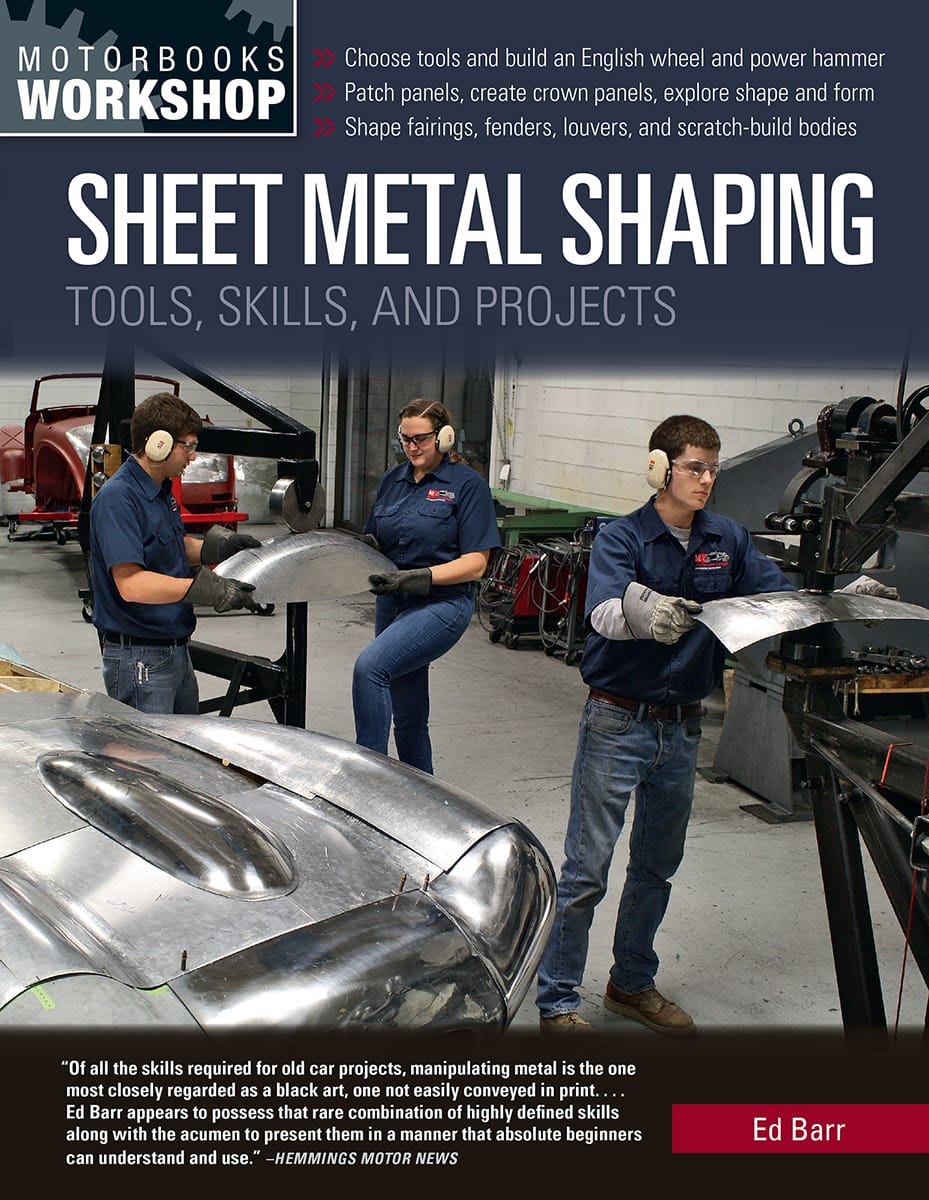
TOOLS, SKILLS, AND PROJECTS
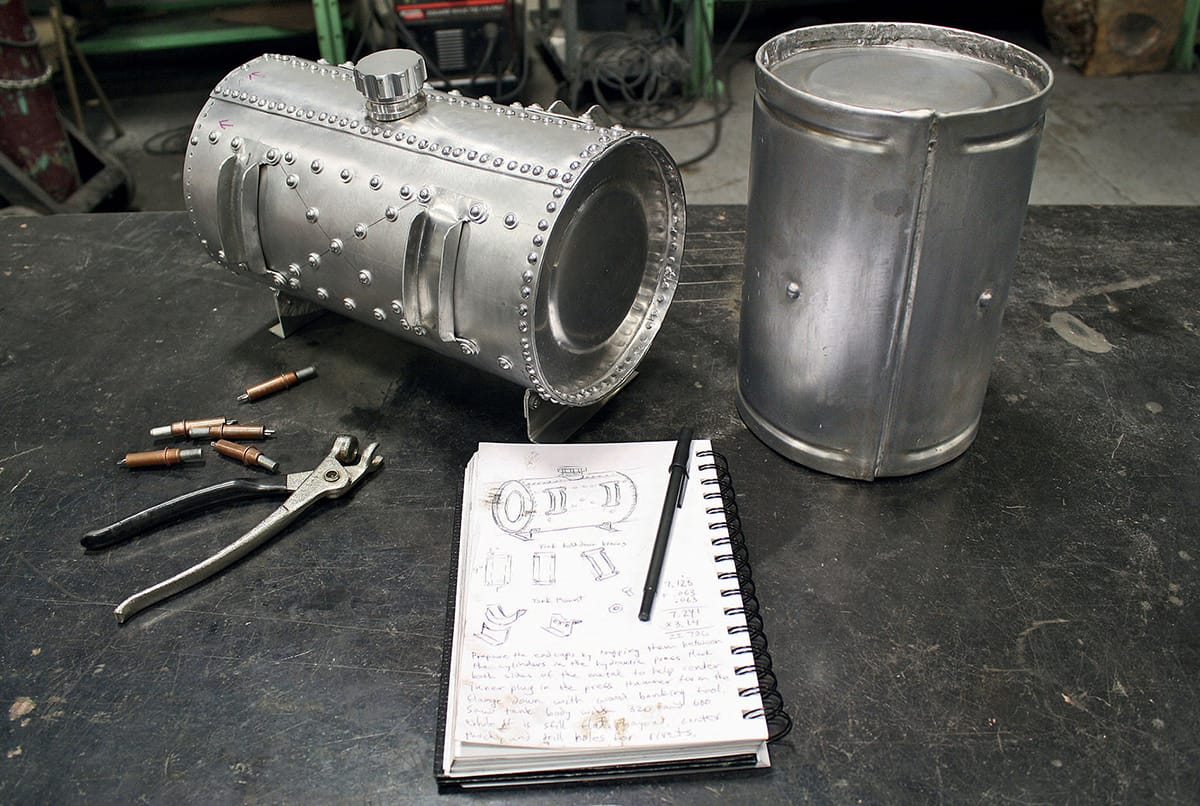
By Ed Barr
M y favorite color is bare metal. I love the tactile sensations that come with working with metal, and I adore the sweet bouquet it gives off when its cut. Most of all, I love the challenge of turning flat sheets of steel and aluminum into car and motorcycle shapes. If you are exploring metal shaping for the first time, you are in for a great adventure. Offering some guidance via this book will be my privilege. If youve shaped metal before, your fire has most likely already been lit. I will gladly pour on more fuel. Take heart in knowing that you are not the only person who ruminates over sheet metal problems when you are supposed to be sleeping.
If you are new to metal shaping or your past experience with this discipline has been frustrating, do not worry. I have included a series of exercises designed to acquaint readers with the fundamentals of this challenging craft. As with drawing or playing a musical instrument, each of us has a different aptitude for performing this activity. Nevertheless, I am convinced that anyone can learn enough to be able to realize some success working with sheet metal.
As you read through this book, I hope you will be pleasantly surprised by how closely the do-it-yourself exercises mirror problems you have struggled with in the past or that you know lie ahead on your project vehicle. I also hope that you find my explanations and proposed solutions clear and easy to follow. As you work through the exercises, think about the results in light of what you have read. What could be improved? Repeat each exercise until you have mastered the concepts. Repetition, coupled with thoughtful analysis, will keep you moving forward. One day you will look back with surprise and satisfaction at what you have accomplished and what you have figured out on your own. You may even find yourself lying awake at night, ruminating on your next sheet metal challenge.
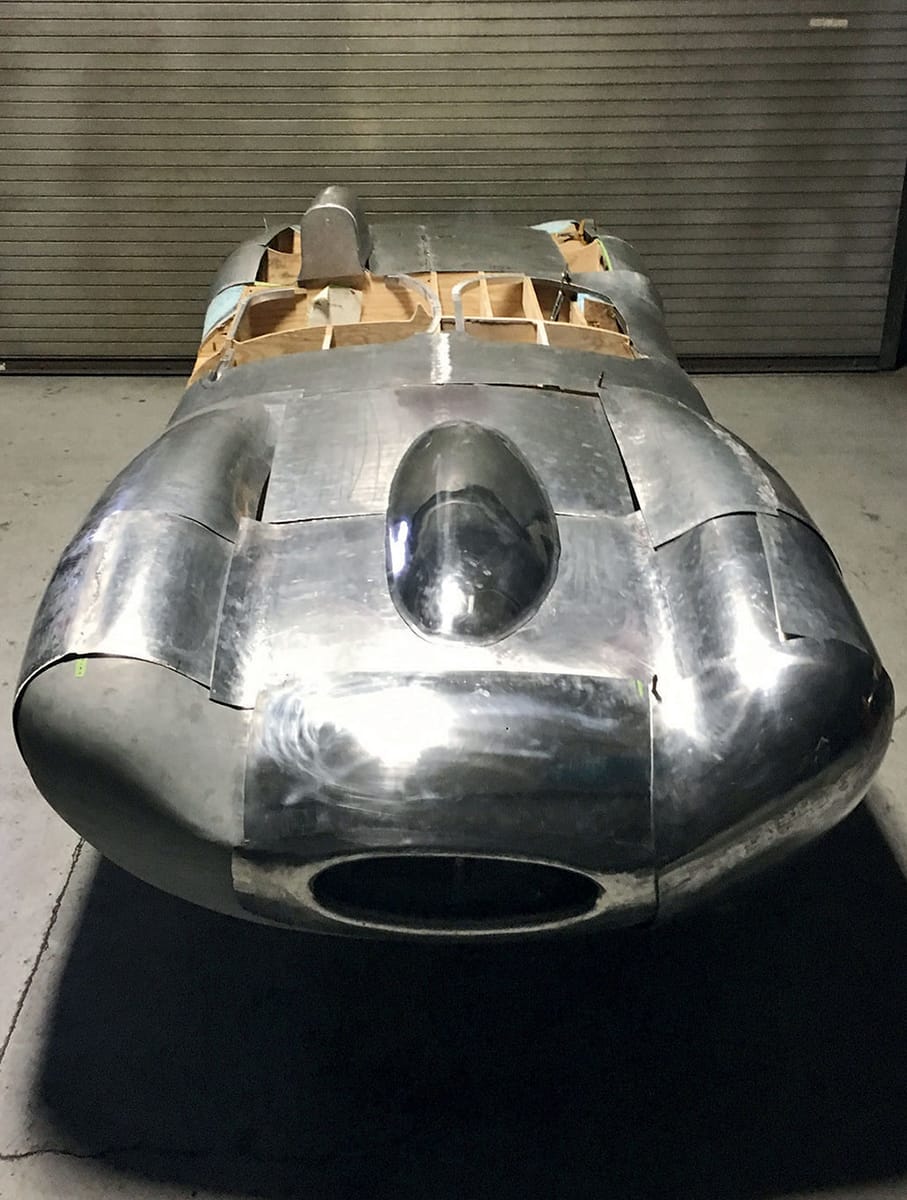
O ne afternoon while waiting in line to pay for medications at the vets office, I searched the internet to see what car I could buy for the amount I spend on dog meds each month. I burst out laughing when I saw a used Maserati. It was even red. Of course, Id rather have giant, aged mastiffs lumbering around the house than a Maserati. The latter doesnt salivate or leave the house smelling like moldy Parmesan cheese (traits you just cant buy), but living costs money, usually a lot of it. If you, like me, are interested in making the most of every penny, here are some tips to help you have fun shaping metal as inexpensively as possible.
In my previous book, Professional Sheet Metal Fab-rication (2013), I discussed tool choices for metal shaping and automotive restoration. At home, my interests lean much more toward shaping and coachbuilding than pure restoration, so I have refined my selection to squeeze more metal-shaping exhilaration into each day. Moreover, while the exhilaration can spill over into both sides of a two-car garage, the tools that make it happen need to be collapsible into one side of our home garage. My wife has sacrificed too much to indulge my appetite for old cars to park out in the cold. Ive built most of an aluminum sports car body using a paltry assortment of tools, so I know it can be done, and not because Im a metal genius. On the contrary, my gifts are enthusiasm and perseverance. Fortunately, those gifts have been enough to keep me gainfully employed. There will always be haters who raise their noses at you for what they perceive you to lack. Ignore them. If you are covered in mastiff slobber and reek like moldy Parmesan, as I do, then they wont come close enough to be critical.
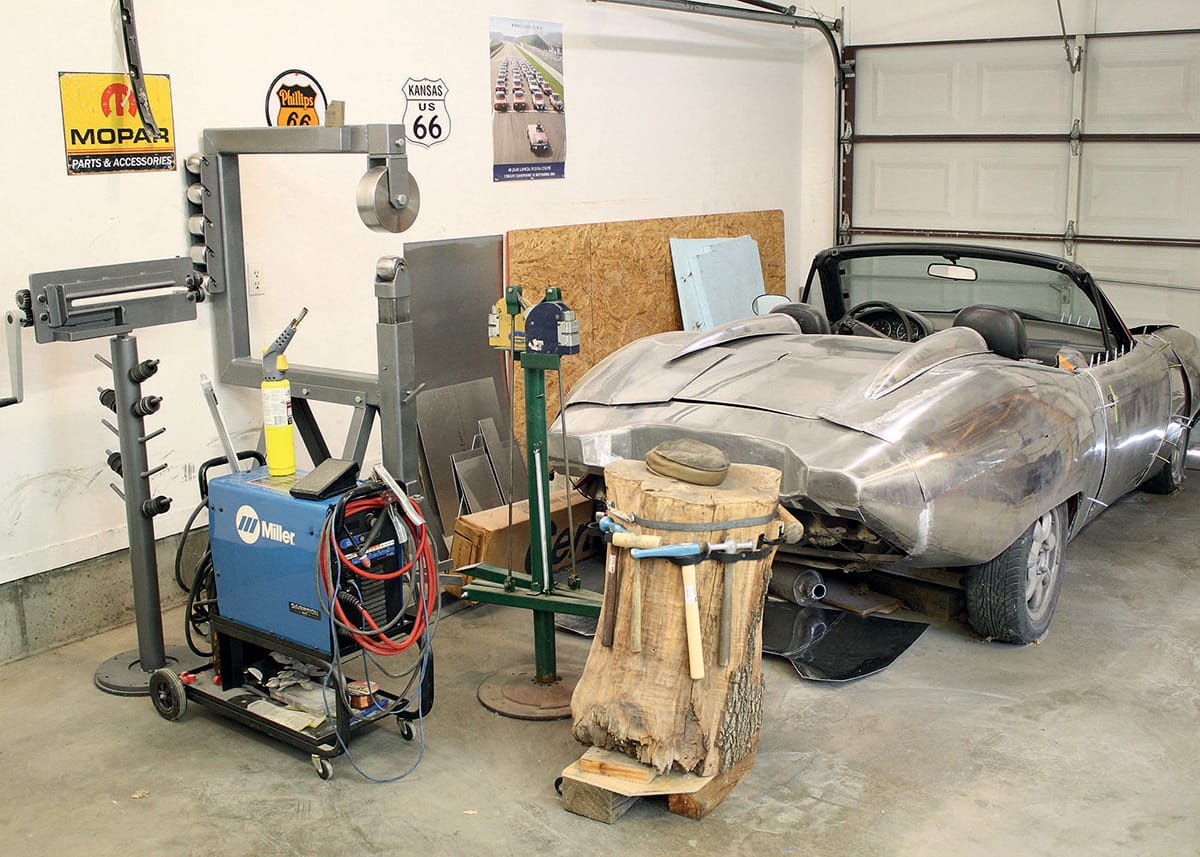
Dont let a dearth of space and tools keep you from realizing your sheet metal dreams. Make the most of what you have. You will be surprised by what you can achieve.
Ironically, being completely spoiled by an embar-rassment of riches at my workplacetwo power hammers, a Pullmax machine, five wheeling machines, sundry other delightshas made me absolutely comfortable with few tools at home. Using aluminum as my chosen material helps. Shaping aluminum with hand tools is much easier than shaping steel, but I would still use the same selection of tools at home if I were working with steel.
The two tools I use the most are a stump and a wheeling machine. I have included a chapter on building your own wheeling machine if you desire, so I will not elaborate on that tool here, other than to say it is a great value for the money and a good choice for the home enthusiast because it is quiet, doesnt require power, and does not have to take up a lot of space.
Although I have a freestanding stump that I got for free, a smaller block of wood could be substituted. In the classroom, I use large rectangular blocks made from tree trunks that can be easily moved around. Wood blocks are also more versatile than a freestanding stump because you have more surfaces to modify. The freestanding stump I use at home has many purposes, not all of them strictly related to shaping. It serves as a welding table, worktable, lunch table, and iPhone stand. Dean Martins voice sounds even more mellifluous when it is projected out of a hollow in a metal-shaping stump.
If, like me, you have almost no workbench space, a freestanding stump might be a better choice than a block of wood that sits on a table. I built a base on the bottom of my stump to keep the top surface stable and level. I also mounted two casters vertically on the back and a handle on the front. I simply tilt the stump back on the casters to roll it about the shop.
In my experience, large blocks of wood tend to dry out over time. When they do, I turn them into firewood and replace them. Because my freestanding stump is a piece of furniture, however, I have gone to the trouble to wrap a steel strap around it that can be cinched tighter with a turnbuckle. In a stroke of environmentally friendly zeal, I recycled a used serpentine belt from my wifes minivan for use as a hammer retention strap.
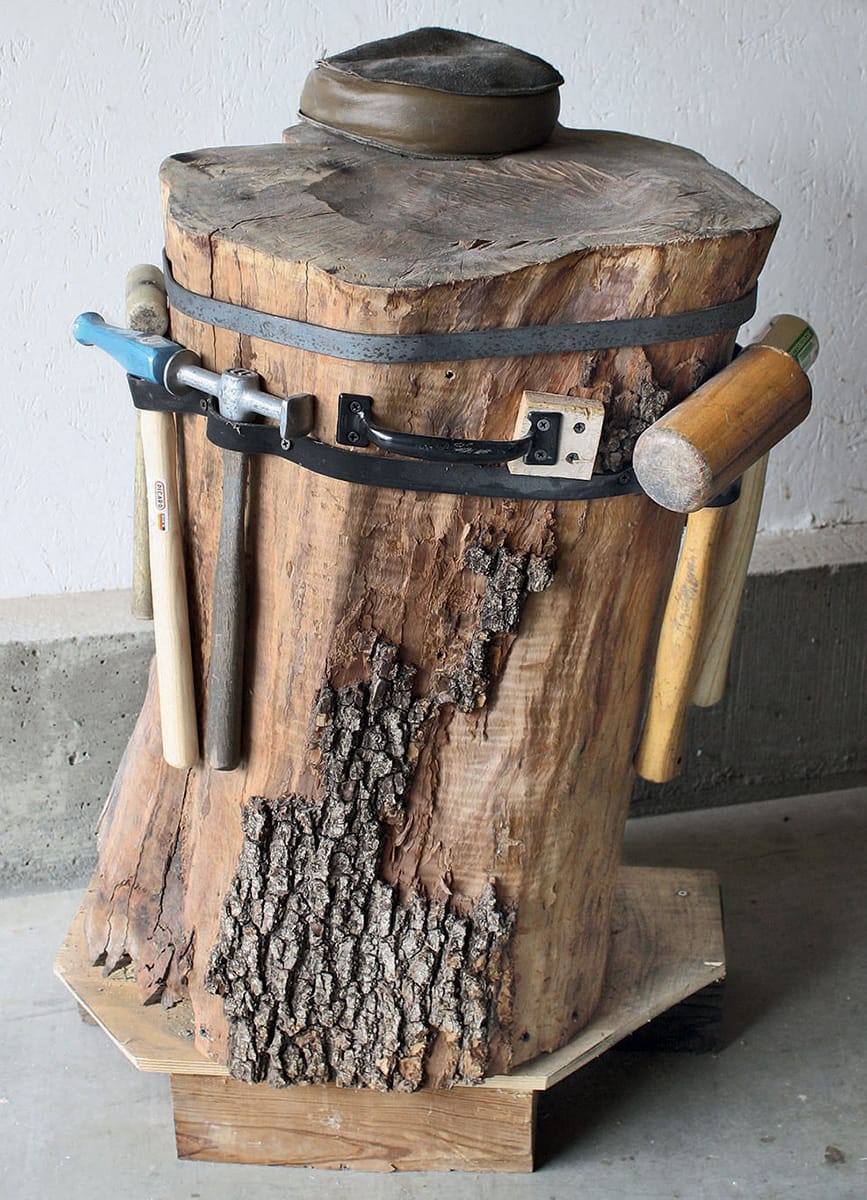
A wooden block will perform most of the shaping duties of a stump, but a freestanding stump might still make sense if you can use it for other purposes, such as a welding table or breakdance platform. The casters mounted vertically on the back and the handle on the front make this one easy to move.
The next tool I frequently use in my home shop is a tucking tool for shrinking metal. I discussed the tucking tool at length in Professional Sheet Metal Fabrication, but I neglected to give directions for making one. Take two of the longest grade eight bolts you can find and cut their heads off. If you have access to a lathe, taper the shafts. If you do not have access to a lathe, spin each bolt in a drill press or drill while you apply a handheld grinding tool to the shaft of each bolt. Tapering the bolts removes the threads so they wont mark the metal and optimizes the tool shape for creating wrinkles or tucks along the edge of a piece of sheet metal. Make the small ends of each tong about as big as the diameter of your pinky finger for your first tucking tool. This size will be sturdy enough for annealed 14-gauge aluminum or 20-gauge steel. You will not be tuck shrinking anything heavier than that unless you are a superhero, and in that case youll be too busy to shape any metal anyway. When you come across an area that needs to be shrunk but the panel will not fit in your Lancaster-style shrinker, a tuck might save the day. If the access is so restricted that the tucking tool will not fit, use a pair of 90-degree pliers to fold a tuck into a panels edge.
Font size:
Interval:
Bookmark:
Similar books «Sheet Metal Shaping»
Look at similar books to Sheet Metal Shaping. We have selected literature similar in name and meaning in the hope of providing readers with more options to find new, interesting, not yet read works.
Discussion, reviews of the book Sheet Metal Shaping and just readers' own opinions. Leave your comments, write what you think about the work, its meaning or the main characters. Specify what exactly you liked and what you didn't like, and why you think so.