THE PROP BUILDERS
MOLDING & CASTING
HANDBOOK
THURSTON JAMES
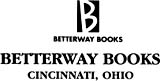
The Prop Builders Molding & Casting Handbook. Copyright 1989 by Thurston James. Printed and bound in the United States of America. All rights reserved. No part of this book may be reproduced in any form or by any electronic or mechanical means including information storage and retrieval systems without permission in writing from the publisher, except by a reviewer, who may quote brief passages in a review. Published by Betterway Books, an imprint of F+W Publications, Inc., 4700 East Galbraith Road, Cincinnati, Ohio 45236. (800) 289-0963. First edition.
Cover design by David Wagner
Typography by Typecasting
Every precaution has been taken in preparing The Prop Builders Molding & Casting Handbook to make these projects as safe and successful as possible. However, neither Betterway Books nor the author assume any responsibility for any damages or injuries incurred in connection with the use of this manual.
Other fine Betterway Books are available from your local bookstore or direct from the publisher.
15 14 13 12 11 22 21 21 19 18
Library of Congress Cataloging-in-Publication Data
James, Thurston.
The prop builders molding & casting handbook / Thurston James.
p. cm. Includes index.
ISBN 13: 978-1-55870-128-1 (pbk.)
ISBN 10: 1-55870-133-8ISBN 10: 1-55870-128-1 (pbk.)
1. Plaster craft. 2. Molding (Founding)Amateurs manuals. 3. PlasticsMoldingAmateurs manuals. 4. Stage propsDesign and construction. I. Title. II. Title: Prop builders molding and casting handbook.
TT295.J36 1989
792'.025dc20 89-36138

Acknowledgments
I am under some obligation to Marsha FrankBurke, editor and author, for her work in editing this series of books on property construction techniques. She helped me to find an order to a very wide ranging subject. As the texts received their first exposure to editing, Marsha unknowingly taught me a subject I refused to take seriously in high school: how to communicate in written English. I am grateful.
I want to thank Rob Secrest, a molding and casting expert from the Albuquerque area. He read a first draft of this text and made many helpful comments. Rob was also available for regular consultation as the final text was being completed.
I am indebted to Nick Bryson, President of Gerriets International, for developing the basic design of the vacuum forming machines which are demonstrated in the final chapter of this book. I appreciate the work done by Jeff Wachtel, Principal Electronic Technician for The Department of Theater at UCLA, as we modified this concept to build a vacuum forming machine specifically for use in producing properties.
LaVahn Hoh of the University of Virginia read, reviewed, and criticized the final manuscript. His careful reading and concerned comments prompted the rewriting of several sections.
I acknowledge The Department of Theater, Film, and Television at UCLA for allowing me to use the theater facilities during my off-duty hours to photograph the properties for our productions as they were being made.
PREFACE
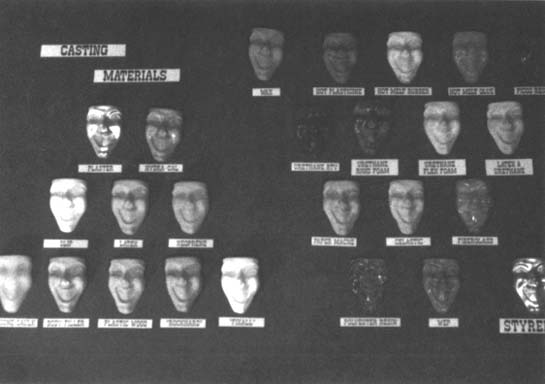
The Materials of Molding and Casting
This book will demonstrate the methods and techniques for using thirty different molding and casting materials, ranging from papier-mch to breakaway glass. No assumption has been made that the reader has any previous experience.
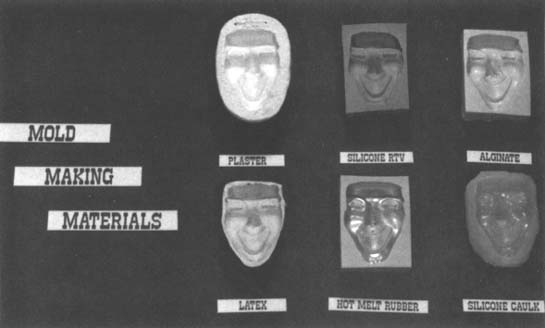
The mold-making materials include plaster, two kinds of alginate, two forms of silicone rubber, latex, and hot-melt rubber.
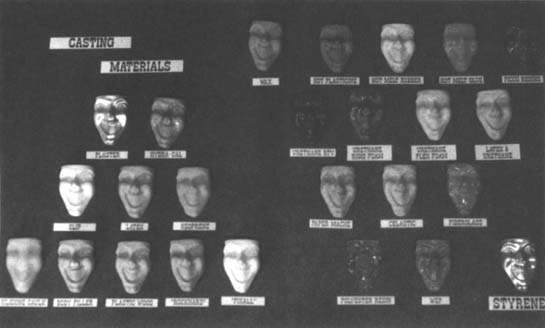
Casting materials long familiar to theater techniciansplaster and its cousins and Celasticare covered with the same thoroughness as the more recent flexible plastics which have been developed: latex and three variations of polyurethane.
Thermosets are discussed with an emphasis on the polyester resins, fiberglass, and water extendable polyester.
A series of materials which become liquid when heated to their melting point is thoroughly demonstrated. The hot melt materials include wax, hot-melt rubbers, and hot-melt picco resins used in the manufacture of breakaway glass.
The section on slipcasting shows how a newer product, neoprene, uses an age-old pottery process to great advantage in the theater.
Products found at local hardware stores in the form of putties and caulking compounds are included, showing their unique features and how they can be pressed into service as casting materials when nothing else is readily available.
Near the end of the book is a section devoted to the construction of a vacuum forming machine. The instructions are intended to aid an experienced electrician and metal worker in the special problems encountered in building this large tool. This is the only portion of text that is not directed to an inexperienced person. The final chapter explains some techniques of using this machine or any of the commercially made vacuum forming machines being found in increasing numbrs in university and community theater scene shops.
How to Get Started
How does a person go about learning the techniques of casting and mold-making? Here are some of the ways:
1. Attend workshops
2. Apprentice with an old timer
3. Jump in, experience trial and error, and learn by doing
4. Read product literature and experience new materials as they come along
5. Read a book
Begin with any of these and work your way through them all. Maybe all of the ways will not be open to you. Thats probably O.K. do what you can. These are all good ways, and they all have their limitations. Lets touch on each of these methods, and discuss some of their advantages and disadvantages.
Workshops
In most cities, hobby shops and plastic suppliers conduct workshops as a means of showcasing their products. If your supplier does not have this service, you might at least arrange for the demonstration of certain specific products you are interested in. The problem with even a well-organized workshop is that there is limited time provided in which to demonstrate a time-consuming subject. In three or four hours you can only be introduced to three or four products, and these only in the most basic fashion. But at least you will have been introduced.
Apprentice with a Working Craftsman
This is a good idea if you have the time and really are serious about learning the craft. Search out a mold maker with some experience, spend some time with him, and pick his brain. Count yourself as very fortunate if you can place yourself with a mold-making craftsman. Keep your mind open, realizing that even experts have prejudices and favorite methods, and very frequently they do not agree with other experts.
I do not believe that mold-making and casting experts are an endangered species. They have just become more specialized. You will find them in the porcelain and ceramics field, in aerospace, as tool and pattern makers, in plastic toys, plastic packaging, and plastic products of all kinds. The motion picture audiences thirst for the bizarre has produced a market for a wide variety of aliens and extraterrestrials. Most of the designers of these monsters are not old timers, they are comparative youngsters. And speaking of youngsters I was recently in the curators workroom at the Museum of Natural History in Los Angeles, where the staff was working with junior high schoolers making latex impressions of delicate tropical ferns for use on the museums wild animal exhibits. The museum was getting a large volume of authentic-looking plastic foliage, and the kids were getting a hands-on experience in the technique of mold-making.