Paul N. Hasluck - Metalworking
Here you can read online Paul N. Hasluck - Metalworking full text of the book (entire story) in english for free. Download pdf and epub, get meaning, cover and reviews about this ebook. year: 2011, publisher: Skyhorse, genre: Children. Description of the work, (preface) as well as reviews are available. Best literature library LitArk.com created for fans of good reading and offers a wide selection of genres:
Romance novel
Science fiction
Adventure
Detective
Science
History
Home and family
Prose
Art
Politics
Computer
Non-fiction
Religion
Business
Children
Humor
Choose a favorite category and find really read worthwhile books. Enjoy immersion in the world of imagination, feel the emotions of the characters or learn something new for yourself, make an fascinating discovery.
- Book:Metalworking
- Author:
- Publisher:Skyhorse
- Genre:
- Year:2011
- Rating:4 / 5
- Favourites:Add to favourites
- Your mark:
- 80
- 1
- 2
- 3
- 4
- 5
Metalworking: summary, description and annotation
We offer to read an annotation, description, summary or preface (depends on what the author of the book "Metalworking" wrote himself). If you haven't found the necessary information about the book — write in the comments, we will try to find it.
Metalworking — read online for free the complete book (whole text) full work
Below is the text of the book, divided by pages. System saving the place of the last page read, allows you to conveniently read the book "Metalworking" online for free, without having to search again every time where you left off. Put a bookmark, and you can go to the page where you finished reading at any time.
Font size:
Interval:
Bookmark:
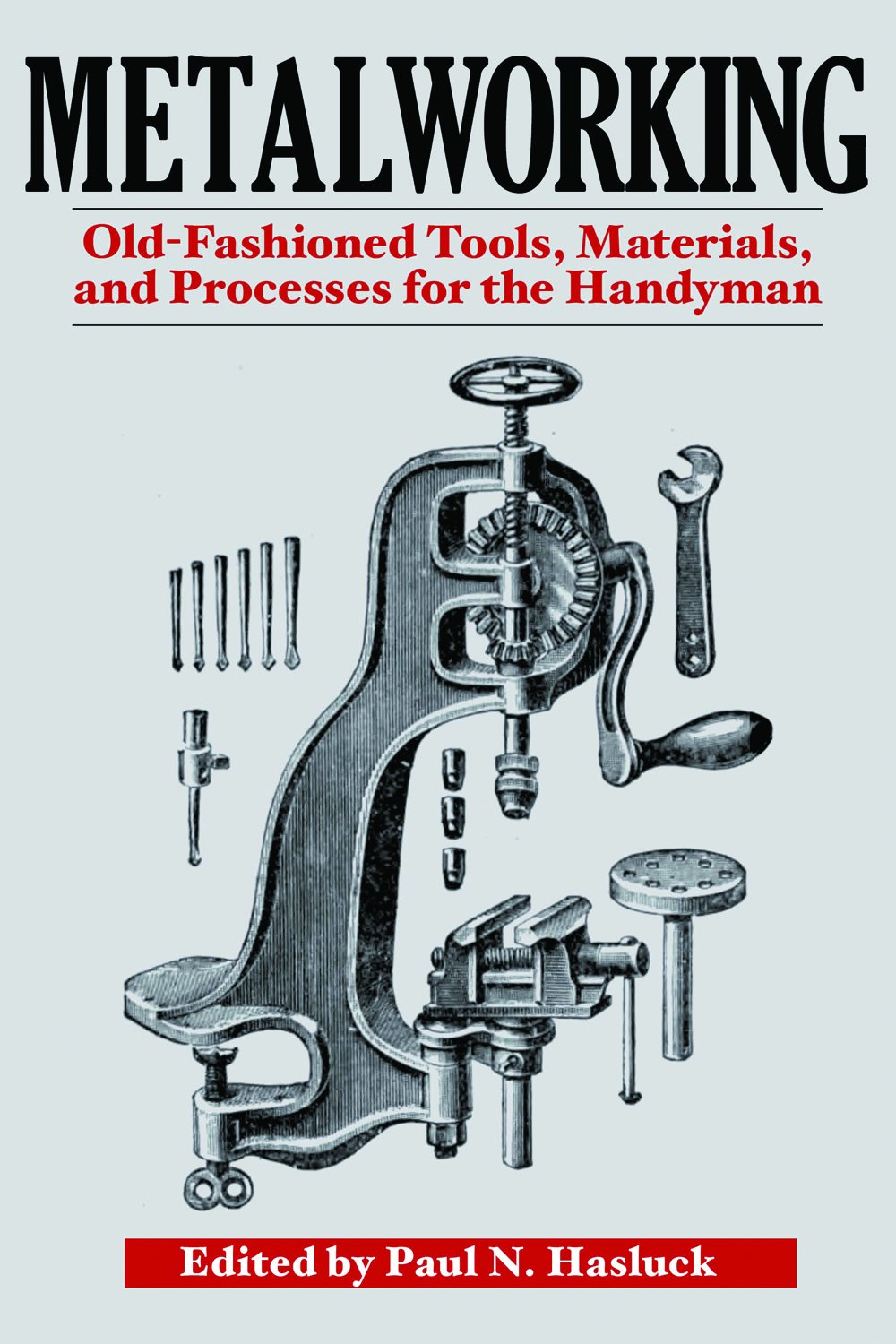
The work of the foundry falls naturally under two principal headsthe metal, and the moulds. In large shops these are two distinct classes of work, performed by different sets of men. In small shops the moulder must often mix and melt his own metal. The metal may be bought ready prepared in ingots ; or the founder may prefer to make his own mixtures. Ingots are convenient, but mixing is cheaper, and the mixer knows what metal he has, which is more than can be said when ingots are bought. An experienced mixer can obtain any grade of metal needed for any class of work, and can use a good deal of waste stuff, together with runners and risers from previous casts.
Aluminium bronze consists of aluminium and copper in varying proportions. A special hard alloy contains 11 per cent. aluminium, and others contain from 10 to 1 per cent. aluminium. The 10 per cent. alloy has a tenacity of about 100,000 lb. per square inch, but shrinks upwards of twice as much as brass. As the metal solidifies rapidly, it is necessary to pour with very large gates, and every precaution must be taken to prevent the metal setting in the gates before the casting has been completely poured. The great difficulty with large cored work is to prevent the metal cracking. This must be done by using baked cores consisting of sand and cinders ground together and just held with a little resin. Aluminium bronze of the above quality oxidises rapidly when poured from the crucible to the mould. If the film or skin of oxide passes into the mould, it will appear on the surface as dirt, and will probably spoil the casting. The scum may generally be kept back by the ordinary skimmer, if the pourer takes special care. As aluminium and copper volatilise only at very great heats, there is no appreciable loss in continued casting. Metal made simply by mixing aluminium and copper will most probably be brittle, and does not acquire its best properties till it has been remelted several times. If the casting is uniformly thin, it will generally come sharp, but, if there are thin and thick parts, it is necessary to put runners or offshoots from the thin parts to enable the metal to fill and soak back into the casting as it cools. This will overcome the difficulty often met of thumbing, or the formation of shallow places at the thick parts of the castings. A good bearing brass is an aluminium bronze containing 95 parts of copper and 5 of aluminium, to which is added 8 per cent. of tin. A good method is as follows :In using a 140-lb. crucible, melt 124 lb. of copper under a good layer of charcoal; then add cautiously, bit by bit, 6 lb. of ingot aluminium, or fairly heavy aluminium scrap. When the metal is quiet, add 10 lb. of ordinary cake tin, thoroughly well stir in, an-d pour into ingots. When making brasses, take about half the weight of the casting required in scrap metal, and make up with the new ingot metal. This, when melted, must be well stirred and then poured. It is necessary to have large gates to allow proper shrinkage, as there is considerable liability to draw. The mould must be rather loosely rammed, and when poured the metal must not be touched for some time, as it remains liquid in the mould longer than the usual alloys.
The metals that form anti-friction or bearing alloys are copper, tin, antimony, zinc, and lead, although more than three rarely enter into any one mixture. To reduce the friction at a journal, a bearing of brass, bronze, or gunmetal is made, and the bearing surface is lined with a white alloy of comparatively soft nature. On account of its low melting point, when the white bearing shows wear it may be melted out, and a fresh lining inserted, the bronze or other frame thus lasting a very considerable time. The metals are generally melted in an iron ladle, and if allowed to get too hot will volatilise, the nature of the alloy being altered, or will oxidise and form a scum that must on no account be allowed to run into the bearing. These white-metal bearings are used for very fastrunning machinery, to prevent the axles or shafts and the brasses heating and consequently binding. Two good anti-friction metals are Babbits metal and magnolia. Babbit recommended melting together 4 lb. copper, 8 lb. antimony, and 24 lb. tin. This he named hardening, and to every pound of it he added 2 lb. tin. Numerous varieties have from time to time been introduced. one being antimony 2 parts, tin 2 parts. lead 20 parts. Magnolia is a white metal composed approximately of lead 78 parts. antimony 21 parts, and iron 1 part; it does not appear to heat when subjected to intense pressure.
Bell metal is the material used in the manufacture of bells, and it consists principally of copper and tin, although for the commoner classes other materials are often used, such as iron, lead, zinc, antimony, and manganese. Bell metal should be hard, compact, fine-grained, and strong, and should be cast in a manner similar to bronze. The copper is first melted, the tin is next added. and, after vigorous stirring, the metal is then poured.
Brass may be considered the most common of the commercial alloys ; it is a compound of copper and zinc in very variable proportions. The commonly used yellow metal consists principally of 60 parts copper and 40 parts zinc, with such slight additions of other metals as are necessary to serve special purposes. This alloy, known as Muntz metal, makes sound castings, and compared to copper is less liable to discolour, is harder, closer in grain, more workable, and fuses at a much lower temperature. The impurities inherent in ordinary copper and zinc are not troublesome in brass foundry works, because it is a general practice to use common brass pigs. For turning work it is well to use 1 lb. of lead to each 100 lb. of molten metal. The molten metal containing the lead must be thoroughly mixed at each pouring, as the lead will liquate or separate out. Common brass used for ordinary bolts, nuts, and turnery work consists of the following mixture : 60 parts copper, 42 parts zinc, and 1 part in the 100 lead. This will work either hot or cold, and forms the usual French alloy. English naval brass, which is stronger than common brass, consists of two qualities, the one used in rolling sheets and rods, the other for making tubes. In the former the alloy is 62 parts copper, 37 parts zinc, and 1 part tin, while in the latter the alloy is 70 parts copper, 29 parts zinc, and 1 part tin. The metals must be thoroughly mixed and stirred before pouring.
The art of mixing alloys for brass can be learned only by practice, but the following broad principles conduce to success. The mixing of the copper alloys becomes the more difficult with increase in the fusibility of the elements. Thus, it is easier to mix hard gun-metal than soft brass, because the zinc in the latter volatilises so rapidly that much of it is liable to be lost in fumes, with considerable diminution in the weight of the alloy, and resulting uncertainty in regard to the composition of the final product. But tin and copper will alloy with little waste, and yield practically certain results. When the soft brasses are required, it is better to mix a large proportion of brass with copper than to make the mixture directly with copper and zinc. When zinc is mixed with copper, the latter must be melted first and the zinc added in small quantities at a time, the surface of the copper being strewn with charcoal powder. Broken glass may be used instead of charcoal dust on the top of molten brass to prevent oxidation. When adding easily fusible metal in fragments to molten copper, they must be perfectly free from moisture, and hot; otherwise the addition will cause a blow up of the melted metal. When blue fumes are given off, that denotes oxidation of the zinc, and the pouring must not be delayed long after. It is better to melt metal at least once, and inget it, than pour it directly into the mould after a first mixing. For the same reason it is good practice to use a considerable proportion of old metal with new. A bit of borax put into the crucible on the addition of zinc diminishes the volatilisation of the latter. When brass turnings are melted up, it is essential that all iron turnings which become mixed with them in the machine shop shall be entirely removed. They would make the brass castings hard and pinny. These are therefore removed with a row of magnets passed repeatedly through the mixture until the magnets cease to take up any more iron.
Font size:
Interval:
Bookmark:
Similar books «Metalworking»
Look at similar books to Metalworking. We have selected literature similar in name and meaning in the hope of providing readers with more options to find new, interesting, not yet read works.
Discussion, reviews of the book Metalworking and just readers' own opinions. Leave your comments, write what you think about the work, its meaning or the main characters. Specify what exactly you liked and what you didn't like, and why you think so.