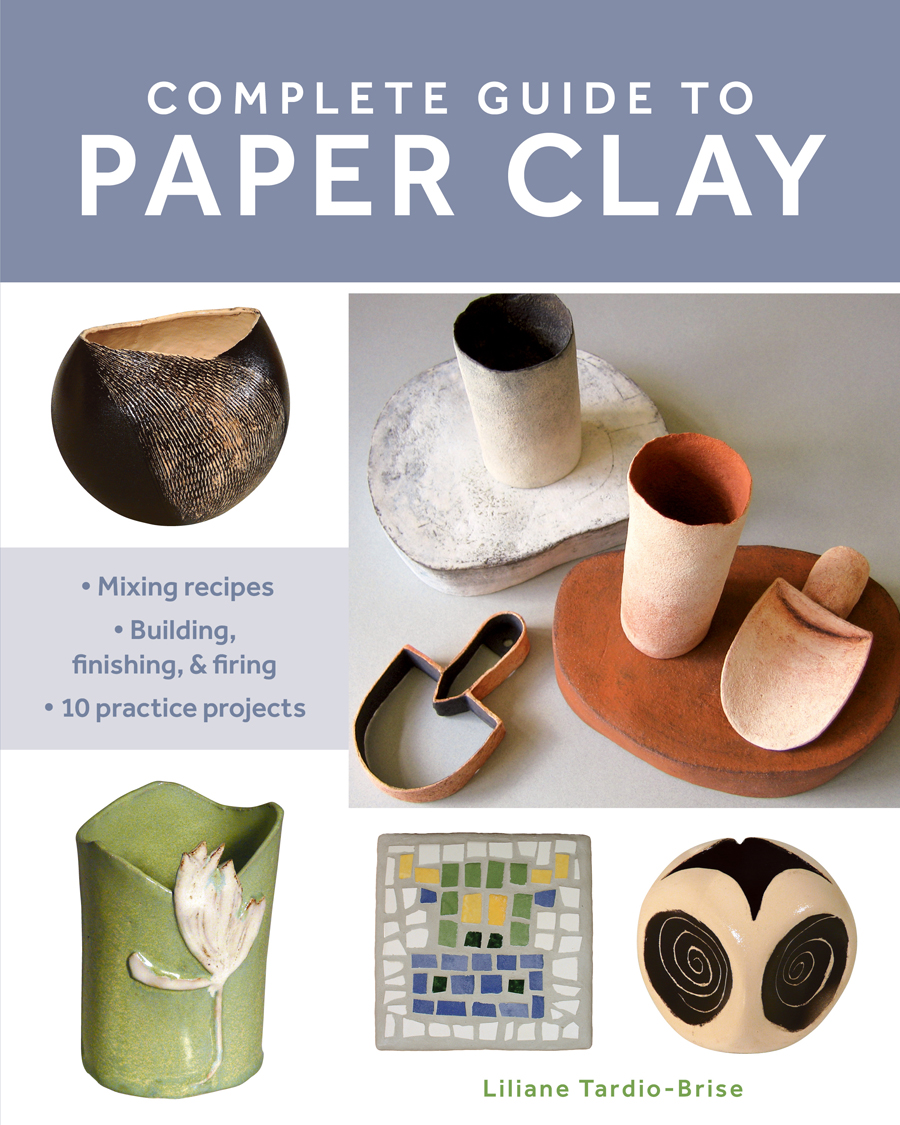
COMPLETE GUIDE TO
PAPER CLAY
To all creators
STACKPOLE BOOKSAn imprint of Globe Pequot, the trade division ofThe Rowman & Littlefield Publishing Group, Inc.4501 Forbes Blvd., Ste. 200Lanham, MD 20706www.rowman.com
Distributed by NATIONAL BOOK NETWORK800-462-6420
Copyright 2022 by ditions Eyrolles, Paris, France
Original French title: La terre-papier 2008, 2016 ditions Eyrolles, Paris, France
Layout: Nord CompoProofreading: Cledon ditions
All rights reserved. No part of this book may be reproduced in any form or by any electronic or mechanical means, including information storage and retrieval systems, without written permission from the publisher, except by a reviewer who may quote passages in a review.
The contents of this book are for personal use only. Projects herein may be reproduced in limited quantities for such use. Any large-scale commercial reproduction is prohibited without the written consent of the publisher.
We have made every effort to ensure the accuracy and completeness of these instructions.
We cannot, however, be responsible for human error, typographical mistakes, or variations in individual work.
British Library Cataloguing in Publication Information available
Library of Congress Cataloging-in-Publication Data available
ISBN 978-0-8117-7069-9 (paper : alk. paper)ISBN 978-0-8117-7070-5 (electronic)
The paper used in this publication meets the minimum requirements of American National Standard for Information SciencesPermanence of Paper for Printed Library Materials, ANSI/ NISO Z39.48-1992.
Table of Contents
Guide
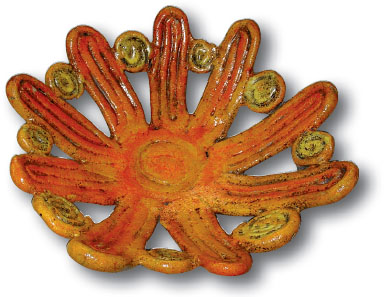
Releasing clay from many of its technical constraints ...
Lightening the pieces ...
Constructing tall, slender shapes...
These things ceramicists dream of become a reality with paper clay.
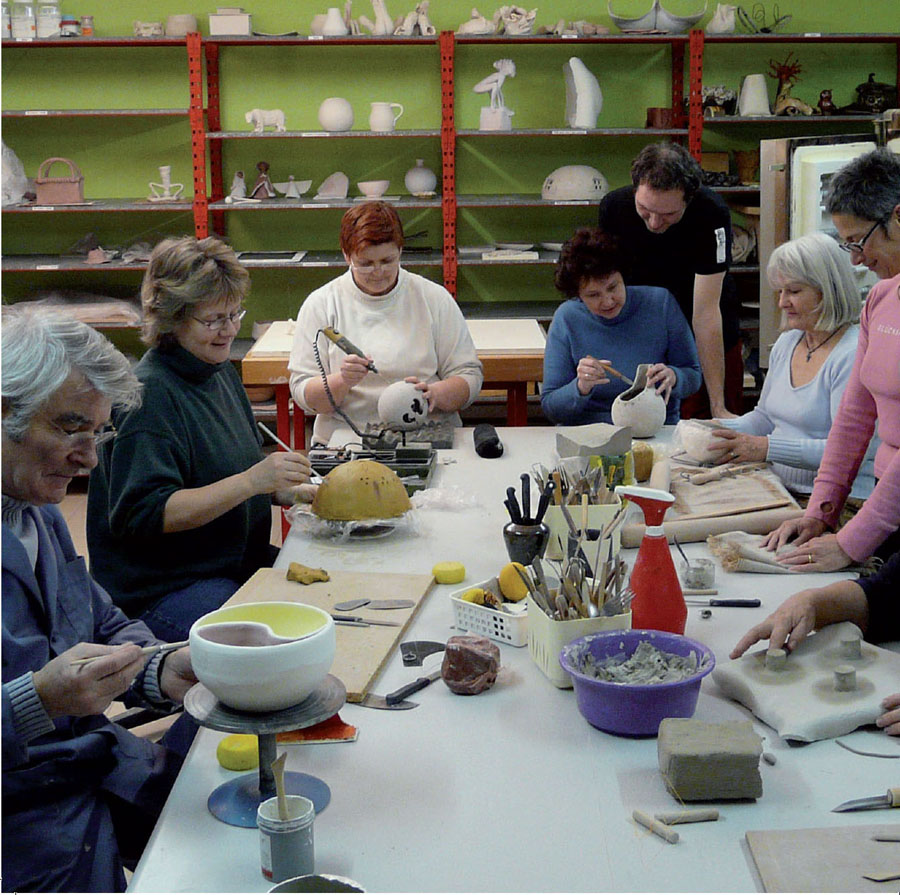
How can adding paper to clay, the heir to thousands of years of tradition, reduce its limitations and constraints to such an extent?
Made from defibered plants, paper has the ability to restore the fibers which, composed of cellulose, have a great affinity for both water and clay. Paper clay is thus a composite material in which the clay constitutes a matrix reinforced by fibers. The addition of plant fragments to give body to the clay is an ancient practice, especially in the construction of adobe or mudbrick houses. But the addition of fibersinfinitely smaller piecesoffers interesting ceramic applications in shaping, finishing, and firing. Since the dry pieces are resistant, firing is not required, and paper clay lends itself to unusual artistic and decorative applications.
The first combinations of clay and paper were made by paper makers who had the idea of depositing kaolin on the surface of the sheets of paper during manufacture to make them smooth and shiny. By introducing clay into the paper pulp, the result is sheets that are somewhat refractory.
Research carried out in the 1980s in Australia by Jaromir Kusnik, a Czech, led to the exhibition in 1987 of decorative panels made from a mixture of clay and fibers. The same year, at the Manufacture de Svres, Jean-Pierre Branger made sheets of porcelain paper on a screen, a method used by paper-making artisans. The tipping of the proportions between clay and fibers, in very clear favor of clay, led to paper clay. This new material really took off in the 1990s, under the impetus of Rosette Gault in the United States, Brian Gartside in New Zealand, and Graham Hay in Australia. In 1998, Rosette Gault published her research in a book entitled Paper Clay and filed a patent in the United States for the marketing of paper clay under the name Pclay.
It is necessary to understand what paper clay is in order to use it wisely and get the most out of it. It shifts away from the technical requirements and discipline of craftsmanship and turns toward artistic expression, as it allows great versatility and freedom of creation. Paper clay is part of the current movement to reuse waste and control energy, since waste paper can be used and a single, quick firing is sufficient.
Paper clay also opens up new horizons for in situ art, which can be dismantled and recycled. Easy to use, followed by simple air-drying, it has its place in introductory workshops, and it opens up new ways of doing things in the area of arts and crafts.
Throughout the pages of this book, you will find practical demonstrations, student pieces, and ceramicists creations, reflecting the leanings of each and the versatility of this material. It is now up to you to discover paper clay, its possibilities and its limits, the fun of working with it, and the many ways it can be used.
Liliane Tardio-Brise
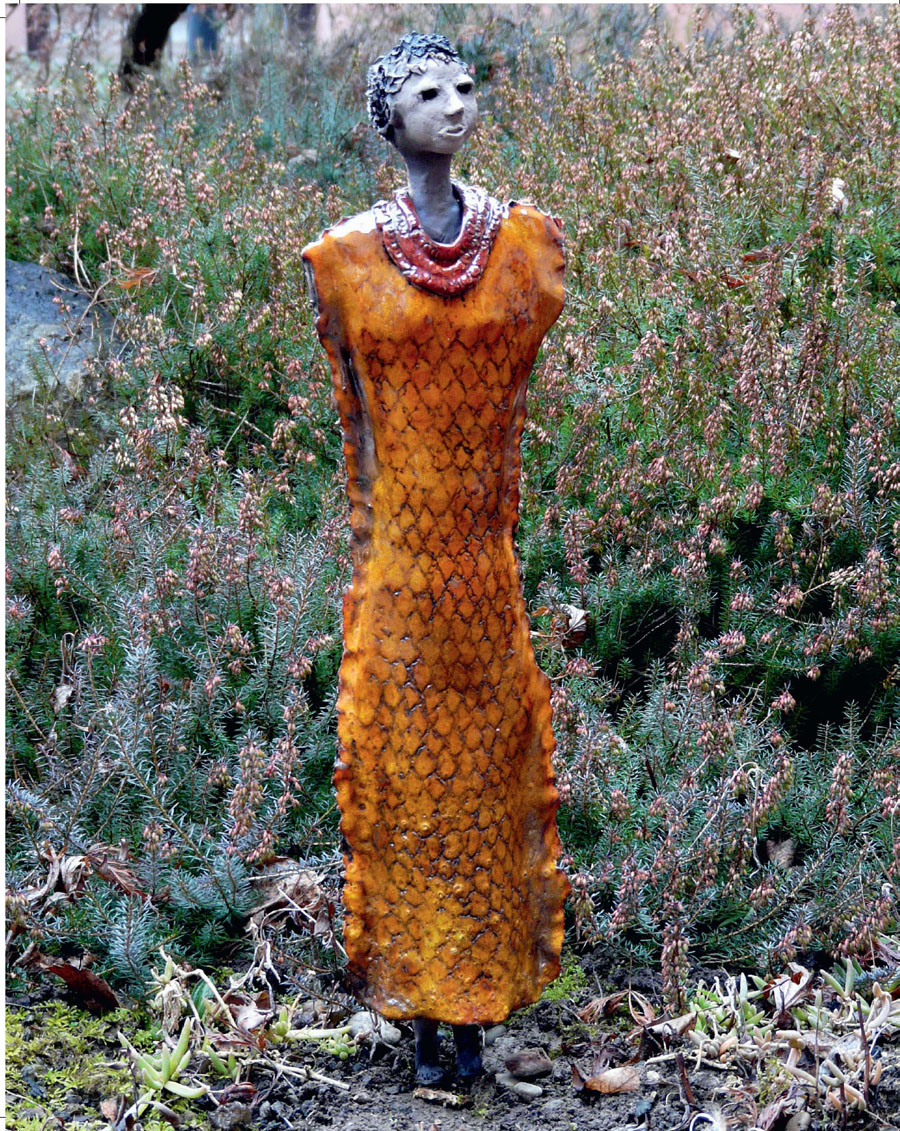
Clay and paper are the two essential components of paper clay. In order to understand the characteristics of these materials, you will find in this chapter a careful study of clay, then of paper, and finally of paper clay.
Packaging labels summarize the information that can be found in greater detail in the catalogs and technical data sheets of ceramic product suppliers.
From a geological point of view, clay is a friable sedimentary rock coming from the erosion of granite. We find clay deposits at all latitudes, deposited by runoff water at the foot of the mountains, in riverbeds, or under arable land. A clay deposit is composed mainly of silica (SiO2)- and alumina (Al2O3)-based minerals chemically bonded by water molecules. The coloring of the mass comes from small quantities of metal oxides and organic debris. The clay has a laminated structure made of hexagonal-shaped platelets. The width of the platelets is on average 0.5 micrometer (1 mm = 1,000 M). Their size decreases the more they are separated from the rocks from which they came. Each deposit therefore has its own particular characteristics: plasticity, color, and melting point.
When the clay is wet, it forms a compact, plastic, and malleable mass: potters clay. Commercial clays, which come in loaves, are ready to use. Some clays will be white, brown, red, or black; others will be frost resistant or refractory. Yet another type will be used for casting, throwing, or hand-building.
The clay body is prepared from one or more clays to adapt it to what the potter wants to use it for. He or she can also improve or compose the mass using mineral raw materials purchased from suppliers of ceramic products. These clays have particular characteristics or minerals that improve the firing process. The different components of a clay body react with each other, and it is by playing with their proportions that we can modify plasticity, shrinkage rate, melting point, and strength of the fired clay. For example:
- the addition of a fine clay improves the plasticity of the body, but increases the drying shrinkage;
- adding alumina raises the melting point;
- the addition of an additive such as grog () reduces shrinkage;
Next page