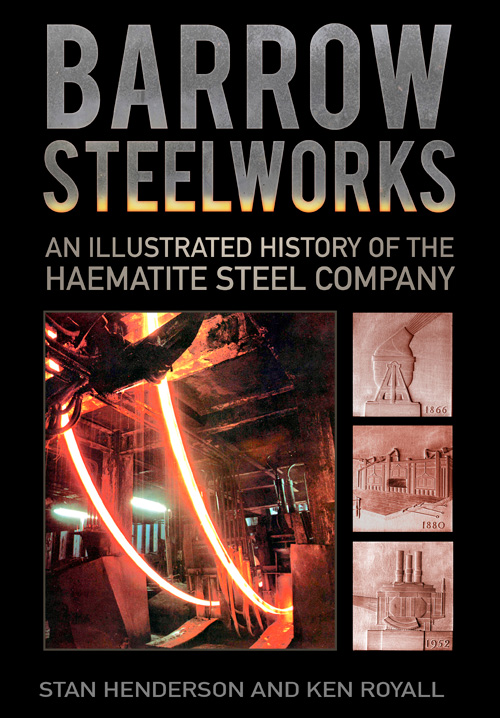
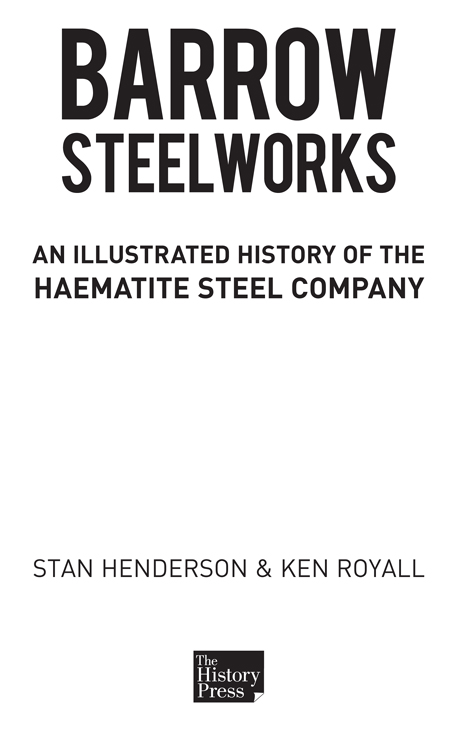
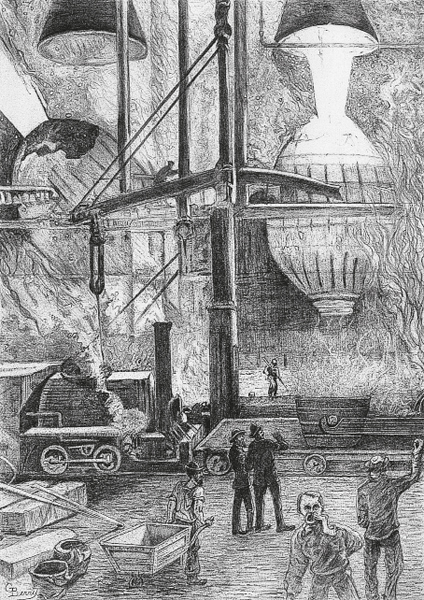
Bessemer steelmaking. (Geoff Berry)
Limitations of space, and thereby cost, have mitigated against the inclusion of all information collated about the works and processes of the British Haematite Steel Company (BHS). More so regarding the Open Hearth process (chapter 6). It is hoped to correct this by the publication of another book a companion to this current work at some point in the future.
This book relies on references to and quotations from several publications. A bibliography of works consulted is included to allow the reader the opportunity for further reading.
I wish to acknowledge the invaluable assistance given by so many who directly or indirectly contributed. I am indebted to my late friend and colleague, George Hurley of the Ship Drawing Office of Vickers, Barrow. George provided my copy of the Iron and Coal Trades Review , which has been the main reference source for the early years of the works. He also related many amusing anecdotes which could easily become the subject of another book.
In particular, I would like to thank Julie Bromley of Corus Rail, Workington who facilitated a visit to the Workington No.1 rail mill in 2002. Also Matthew Roylance for his editing skills, and all that such necessitated.
Grateful thanks to ex-Barrow steelworkers Derek Barnes, Albert Brennan, Jim Ducie, Tony Frankowski, Jim McGlennon, Peter Keenan, Ken Law, Ray Millard, Billy Miller, Bill Pearson, and Jim Walton, who between them have over 300 years experience on which to draw.
Acknowledgements are made to the staff of Cumbria Archives and Local Studies Centre (Barrow), Bill Myers and the Barrow Evening Mail and Sabine Skae of the Dock Museum. The Barrow coat of arms is used under open data from Barrow Borough Council, 19 May 2011.
All photographs used in this book, unless stated otherwise, were taken by K.E. Royall, manager of the Fuel and Instrument Department (also the works photographer from 1957), or sourced from his extensive collection. Every attempt has been made to contact copyright holders. Plate negatives (12x10) now reside at the Dock Museum.
Contents
This book is an attempt to write a local industrial history, at grass-roots level, which may be of value to a new generation of students. It is not about the founding fathers or the rich mine owners of whom much has already been adequately documented. Neither is it an economic history. The book is about the buildings, plant and machinery that collectively comprised the once-mighty Haematite Steel Company at Hindpool. It is also about the men and women with brains and ingenuity and the men whose sweat and aching muscles ran the mills and furnaces of this once colossal works. The project has been an undertaking pursued by the authors in an attempt to preserve the memory of the once prominent local iron and steelworks, and the lives of some of the many who contributed to the works having the unique distinction of twice being a world leader in steelmaking technology nearly 100 years apart. The Iron and Coal Trades Review of 4 August 1899 noted:
Barrow works of the first magnitude were erected to stand or fall by the manufacture of Bessemer steel, and primarily of the rolling of that steel into rails, which had been done nowhere else. It was a bold experiment. The conditions under which the rail manufacture was carried on were hardly sufficiently fixed to determine whether it would be entirely successful. The only rails previously made in England had been treated as cast steel and hammered from ingots 7 or 8 inches square and 4 feet long in four heats. It was some time later before the size of the ingot was raised to a sufficient size to make two thirty feet rails. By the 1870s ingots at Barrow are produced of 5 and 2-tons in weight, and the mills are capable of rolling rails 250 feet in length. The only limiting factor being the amount of metal the Hindpool furnaces could deliver.
Many years later, during the 1950s, the aforementioned ingots would be tossed onto the proverbial scrapheap when Barrow works developed a high-speed process for the continuous casting of steel billets and slabs. This high-speed process consigned several steps of orthodox steelmaking to the history books. Barrow once again played host to the worlds steelmaking fraternity as delegates from steelworks as far away as Japan came to the town, in much the same way as they had in 1874 when Andrew Carnegie and the Iron and Steel Institute came to Barrow. The unfortunate thing was the achievement did nothing to boost the towns economy, or for jobs locally. Taking the broader view, the successful development work in Barrow was part of the biggest improvement in steelmaking since the Bessemer process itself. It may be of interest to note that the casting speeds achieved at Barrow during the 1950s are still an unbroken record.
The idea for this book was hatched in 1984, after having salvaged various items from a skip on the demolition site, which would be visited almost daily. I suppose that like many others I found it hard to accept that it would soon be gone, having grown up in the shadows of its tall chimneys, rumblings, screaming furnaces and general daily commotion. It was assumed that, like Black Combe in the background, it would stand forever.
There are still several gaps in our knowledge with regard to the early history of the works and then the interwar years. Unlike Workington Iron and Steel Company, very little has been recorded or survived for posterity. By far the best reference source is the Iron and Coal Trades Review of 4 August 1899, the narrative of which was copied verbatim in the report of the Iron and Steel Institute visit to the town in 1903, then again in the 1937 book Barrow Steel. The reasons for the production of the latter publication have always been a mystery. This book, which makes reference to being a modern steelworks (which it certainly wasnt), was issued just two years before it was poised to close down but for the onset of the Second World War it most certainly would have. Was this book, then, intended to stand as something of a memorial to a glorious past?
It is not possible in this type of book to give an account of all plant and machinery, which for a period of over 100 years was being constantly upgraded, replaced or rearranged; such a book would take on encyclopaedic proportions, or become just one large engineering inventory. The authors therefore have focused on items, hopefully, of historical significance.
During the thirty years spent collecting information it has not been possible to ascertain the location of the metal mixer, details of the slitting mill, tin bar mill or tyre mill. We do not know precisely when steelmaking by the Bessemer process ceased. It is a fact that whilst the place was an integrated steelworks it was not designed that way. The steelmaking side, east of the Furness Railway main line, was in fact a bolt-on, being laid down six years after the ironworks was established. This meant that the transporting of molten iron between blast furnaces and converters was not ergonomically sound, a journey of over 1 mile being involved for the ladle cars. At Moss Bay, Workington the same journey for the ladles was about 150yds.
S. Henderson, 2014
1
Q ueen Victoria died on 22 January 1901 and she had reigned as Queen of the United Kingdom since 1837 when she succeeded William IV. During her reign massive advances were made in technology and there was a worldwide expansion of boundaries due to the development of railways, heavy engineering and telegraphic communication. Her long reign spanned the second part of the Industrial Revolution and locally the period of what was Barrows greatest development. The most significant early effects of this progress were in the areas of the Strand and Hindpool. Hindpool became home to many local industries, and by far the largest and most significant was the iron and steelworks, aided in no small measure by the Furness Railway Company. From the excellent 1958 work of Dr J.D. Marshall we learn that the land at Hindpool, which became the site of the iron and steelworks, was bought by the Furness Railway Company from the Cranke family of Urswick.
Next page