Thermal Deformation in Machine Tools
About the Editor
Yoshimi Ito, Dr.-Eng., C Eng., FIET, is Professor Emeritus at the Tokyo Institute of Technology, immediate past vice president of the Engineering Academy of Japan, and past president of the Japan Society of Mechanical Engineers, Tokyo. The author of numerous engineering research papers and books, he is currently involved in the establishment of the Indian Institute of Information Technology, Design & Manufacturing, Jabalpur, India.
Thermal Deformation in Machine Tools
Edited by Yoshimi Ito
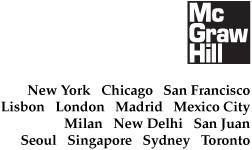

Copyright 2010 by The McGraw-Hill Companies, Inc. All rights reserved. Except as permitted under the United States Copyright Act of 1976, no part of this publication may be reproduced or distributed in any form or by any means, or stored in a database or retrieval system, without the prior written permission of the publisher.
ISBN: 978-0-07-163518-9
MHID: 0-07-163518-1
The material in this eBook also appears in the print version of this title: ISBN: 978-0-07-163517-2, MHID: 0-07-163517-3.
All trademarks are trademarks of their respective owners. Rather than put a trademark symbol after every occurrence of a trademarked name, we use names in an editorial fashion only, and to the benefit of the trademark owner, with no intention of infringement of the trademark. Where such designations appear in this book, they have been printed with initial caps.
McGraw-Hill eBooks are available at special quantity discounts to use as premiums and sales promotions, or for use in corporate training programs. To contact a representative please e-mail us at bulksales@mcgraw-hill.com.
Information contained in this work has been obtained by The McGraw-Hill Companies, Inc. (McGraw-Hill) from sources believed to be reliable. However, neither McGraw-Hill nor its authors guarantee the accuracy or completeness of any information published herein, and neither McGraw-Hill nor its authors shall be responsible for any errors, omissions, or damages arising out of use of this information. This work is published with the understanding that McGraw-Hill and its authors are supplying information but are not attempting to render engineering or other professional services. If such services are required, the assistance of an appropriate professional should be sought.
TERMS OF USE
This is a copyrighted work and The McGraw-Hill Companies, Inc. (McGraw-Hill) and its licensors reserve all rights in and to the work. Use of this work is subject to these terms. Except as permitted under the Copyright Act of 1976 and the right to store and retrieve one copy of the work, you may not decompile, disassemble, reverse engineer, reproduce, modify, create derivative works based upon, transmit, distribute, disseminate, sell, publish or sublicense the work or any part of it without McGraw-Hills prior consent. You may use the work for your own noncommercial and personal use; any other use of the work is strictly prohibited. Your right to use the work may be terminated if you fail to comply with these terms.
THE WORK IS PROVIDED AS IS. McGRAW-HILL AND ITS LICENSORS MAKE NO GUARANTEES OR WARRANTIES AS TO THE ACCURACY, ADEQUACY OR COMPLETENESS OF OR RESULTS TO BE OBTAINED FROM USING THE WORK, INCLUDING ANY INFORMATION THAT CAN BE ACCESSED THROUGH THE WORK VIA HYPERLINK OR OTHERWISE, AND EXPRESSLY DISCLAIM ANY WARRANTY, EXPRESS OR IMPLIED, INCLUDING BUT NOT LIMITED TO IMPLIED WARRANTIES OF MERCHANTABILITY OR FITNESS FOR A PARTICULAR PURPOSE. McGraw-Hill and its licensors do not warrant or guarantee that the functions contained in the work will meet your requirements or that its operation will be uninterrupted or error free. Neither McGraw-Hill nor its licensors shall be liable to you or anyone else for any inaccuracy, error or omission, regardless of cause, in the work or for any damages resulting therefrom. McGraw-Hill has no responsibility for the content of any information accessed through the work. Under no circumstances shall McGraw-Hill and/or its licensors be liable for any indirect, incidental, special, punitive, consequential or similar damages that result from the use of or inability to use the work, even if any of them has been advised of the possibility of such damages. This limitation of liability shall apply to any claim or cause whatsoever whether such claim or cause arises in contract, tort or otherwise.
Preface
Within a machine tool context, there are two crucial technological issues. One is thermal deformation and the other is chatter. Since the 1940s, these two technological subjects have been primary concerns in both production and utilization of technologies for machine tools. We have endeavored to establish the effective remedies for the reduction of thermal deformation and suppression of chatter vibration from both academic research and practical applications. To our regret, even now the remedies available are not totally satisfactory. In other words, while thermal deformation and chatter are very old problems, they still present new technological challenges.
The root cause of difficulties lies in the holistic or synergistic influences of various factors in problems of thermal behavior and chatter. We must solve these problems from the viewpoint of the machine-tool-work system while considering the individual problem of the machine tool, the cutting tool, and the work; whereas, in modular design and lightweighted structural design, the objective is the machine tool itself. Nevertheless, the better functionality and performance of a machine tool itself, the easier it is to establish effective remedies to reduce thermal deformation and suppress chatter.
Importantly, the fundamentals of thermal deformation are transparent considerably relative to those of chatter vibration. For example, thermal elongation is as commonly reported as it has always been and dominant in discussions of thermal deformation. (Academic research has so far concentrated on thermal contact resistance.) In contrast, a considerable number of factors that influence thermal behavior of a machine-tool-work system exist; e.g., heat dissipation capacity from the surface of the structural body component and from the rotating chuck. These factors play very complicated and mutually tangled roles in determining the thermal behavior of a system. As a result, we have not been able to establish perfectly effective remedies, although we can apply a large number of remedies for reducing thermal deformation in practice.
It is desirable in an effective remedy that thermal behavior of a machine-tool-work system, or at least the machine tool itself, be estimated in the design stage. To meet such a desire, there are two crucial subjects to estimate authentically the thermal behavior of the machine tool: (1) dynamic and thermal boundary conditions of the machine tool and (2) heat dissipation capacity from the machine tool to the surrounding environment. Obviously, these two are important target subjects for academia, although corresponding research has not been active.
More specifically, there is a two-pronged perspective in considering the thermal behavior of a machine tool:
1. Design principle for lightweighted structural body component; e.g., realization of a lightweighted structure by using a structural material with a smaller thermal expansion coefficient.
2. The NC machine tool benefits, on one hand, to reduce thermal deformation using compensation technology, but on the other hand, deteriorates the thermal characteristics of the machine tool by, for example, increasing heat sources.
Next page