DISCOVERING JAPANESE
HANDPLANES
DISCOVERING JAPANESE
HANDPLANES
Why This Traditional Tool Belongs in Your Modern Workshop
Scott Wynn
Author of Getting Started with Handplanes
ACKNOWLEDGMENTS
To my father, Jerry, who taught me always to watch and listen; and to my daughter, Josephine, who stands on her grandfathers shoulders watching, listening, and learningand teaching all of us.
I would also like to acknowledge the untiring support of Kathy Tam, the helpful guidance of technical editor Rick Mastelli, and the encouragement and long hours of Jerry Konicek, whose Woodworking Academy gave me the opportunity to verify and refine my techniques.
All illustrations by Scott Wynn.
Photos by Rick Mastelli, Scott Wynn, and Mike Mihalo.
2017 by Scott Wynn and Fox Chapel Publishing Company, Inc., Square Street, Mount Joy, PA 17552.
Discovering Japanese Handplanes is an original work, first published in 2017 by Fox Chapel Publishing Company, Inc. Portions of this book appeared in Woodworkers Guide to Handplanes by Scott Wynn. The drawings and illustrations contained herein are copyrighted by the author. Readers may make copies for personal use. The drawings and illustrations, however, are not to be duplicated for resale or distribution under any circumstances. Any such copying is a violation of copyright law.
Print ISBN 978-1-56523-886-2
eISBN 978-1-60765-938-9
Library of Congress Cataloging-in-Publication Data
Names: Wynn, Scott.
Title: Discovering Japanese handplanes / Scott Wynn.
Description: East Petersburg : Fox Chapel Publishing, [2017] | Includes index.
Identifiers: LCCN 2017003864 | ISBN 9781607659389 (pbk.)
Subjects: LCSH: Woodwork. | Planes (Hand tools)--Japan.
Classification: LCC TT186 .W958 2017 | DDC 684/.082--dc23
LC record available at https://lccn.loc.gov/2017003864
To learn more about the other great books from Fox Chapel Publishing, or to find a retailer near you, call toll-free 800-457-9112 or visit us at
CONTENTS
INTRODUCTION
CHAPTER 1: OF THE
The Blade
A Primer on Steel
The Chipbreaker
The Dai
Reliability
CHAPTER 2: A
Techniques for Achieving Best Performance
Angle of the Blade
Blade Steels for Different Woods
Blade Angles for Different Woods
The Japanese Blade
Pitch Angles
Mouth Opening
Chipbreaker
Japanese Chipbreakers
Bevel Angle
The Correct Bevel Angle
How an Edge Dulls
Honing a Hollow-Ground Bevel
Plane Geometry: A Summary
Shape of the Blade Edge
Length of the Plane/Width of the Blade
The Proportion of Length to Width
CHAPTER 3:
The Jack, Jointer, and Smoothing Planes
Jack: Shaping and Dimensioning
Jointer: Truing
Smoothing
Jack Variations
The Ideal Edge Shape
CHAPTER 4: FOR
Rabbet Planes
Using the Fillister Plane
Side-rabbet Planes
CHAPTER 5: FOR
Compass Planes
Western Versus Japanese Planes for Curves
Using a Compass Plane
The Correct Sole Configuration
Hollows and Rounds
Hollows & Rounds
Other Shaping Planes
Block Plane, Then Chamfer
CHAPTER 6:
Bench Planes
Flattening the Back of the Plane Blade
Tapping Out a Japanese Blade
Gauging Straightness
What Really Happens
The Oiler
Winding Sticks
Adjusting a Japanese Plane
Setting Up Rabbet Planes
Setting Up Side-rabbet Planes
Setting Up Hollows and Rounds
Troubleshooting
Efficient Planing
Keep Your Eyes on the Prize
A Well-Tuned Plane
Keep the Surface Flat
CHAPTER 7:
Jig Drawbacks
Bevel Shape
Grinding
Grinding Out a Nick
Grinding on a Sanding Belt
Sharpening Stones
Listening
Stone Choices
Using and Maintaining Waterstones
Sharpening
Technique
CHAPTER 8: THE
Simple Stop
A Simple Bench
CHAPTER 9: AND
Making a Japanese-style Plane
Laying Out a Block for a Japanese Plane
Chiseling the Chipwell, Mouth & Blade Seat
Making Chibi-Kanna
Making a Compass Plane
Hollowing, Rounding, and Spoonbottom Planes
Laying Out a Block for Hollowing and Rounding Planes
Cutting a Block for Hollowing and Rounding Planes
Laying Out and Cutting the Mouth Opening for Hollowing and Rounding Planes
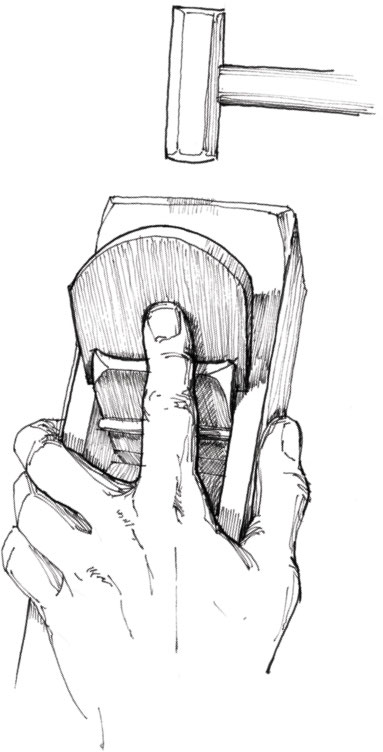
INTRODUCTION
I began woodworking in the late 1960s, a move to be expected, I suppose, because I was raised in a family of cabinetmakers, patternmakers, turners, gunsmiths, and house builders. I felt it was a logical extension of the hands-on building design work I was doing at the time. I picked up what tools I could from the local hardware store and what tips I could from my relatives and a few scattered, scarce written sources. The tools available at that time were immediately disappointing. These were not the tools that built the works of art in the museums. Certainly over the course of 3,000 or more years of woodworking, our predecessors, who did all of their work by hand, had developed effective ways to maximize their efforts to produce flawless work. The hand tools available to me at that time were not capable of flawless work by any means, and what they could do took backbreaking, hand-blistering effort.
I began to look further afield, searching the available sources. In the early 1970s, I drove across the country from my home in Ohio to Berkeley, Calif., to search out an obscure Japanese-tool dealer to look at what were then exotic tools. (The drawings of them in the Whole Earth Catalog looked too bizarre to be real!) Those tools were a revelationand a validation. Japanese tools were meant to be used, used hard, and to produce rapid, excellent results. Well-made hand tools could be a joy to use and be highly productive! I began experimenting with any I could get my hands on, identifying strengths and weaknesses, and the work for which were best suited. Moreover, I used them daily to make my living.