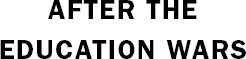
ALSO BY ANDREA GABOR
The Man Who Discovered Quality
Einsteins Wife
The Capitalist Philosophers
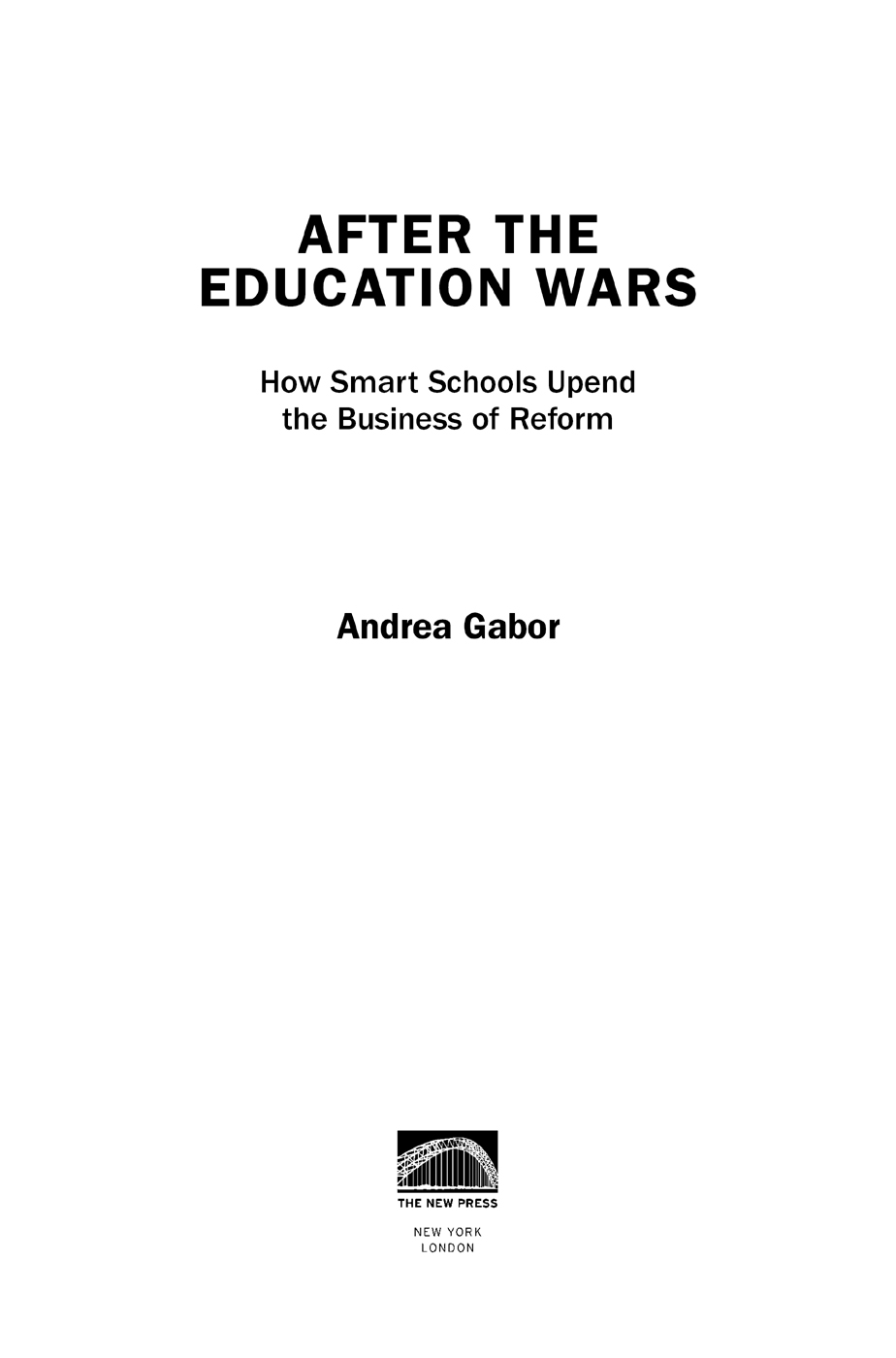
2018 by Andrea Gabor
All rights reserved.
No part of this book may be reproduced, in any form, without written permission from the publisher.
Requests for permission to reproduce selections from this book should be mailed to: Permissions Department, The New Press, 120 Wall Street, 31st floor, New York, NY 10005.
Flowers Are Red, Words and Music by HARRY CHAPIN. 1979 FIVE JS SONGS.
All Rights Administered by WB MUSIC CORP. All Rights Reserved. Used by Permission of ALFRED PUBLISHING, LLC.
Published in the United States by The New Press, New York, 2018
Distributed by Two Rivers Distribution
ISBN 978-1-62097-200-7 (e-book)
CIP data is available
The New Press publishes books that promote and enrich public discussion and understanding of the issues vital to our democracy and to a more equitable world. These books are made possible by the enthusiasm of our readers; the support of a committed group of donors, large and small; the collaboration of our many partners in the independent media and the not-for-profit sector; booksellers, who often hand-sell New Press books; librarians; and above all by our authors.
www.thenewpress.com
Composition by dix!
This book was set in Minion
10 9 8 7 6 5 4 3 2 1
For Sarah, Annie, and Jose.
And in memory of Magda and Imre;
I think of you every day.
CONTENTS
Table of Contents
Guide
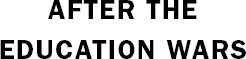
Detroit, 1979. U.S. auto companies were being threatened by foreign competition, and the Motor City became a symbol of American industrial decline. Chrysler would be subjected to its first (but not last) government bailout; the Ford Motor Co. was about to lose $1 billion for that fiscal year, and at least as much again in 1980; and GMs profits were expected to plunge by a breathtaking $2.5 billion. Meanwhile, Japanese automakers were gaining market share; Toyota would soon surpass GM as the worlds largest car company. (A similar scenario played out in other industries too, especially consumer electronics and the copier industry.)
Then, as now, the convenient scapegoat was the rank-and-file employeesin Detroits case, the unionized workers whose relatively high wages and ostensibly poor work ethic were initially blamed for the automakers problems. Only as Japanese wage rates reached parity with those in the United States and Japanese automakers began hiring American workers for their U.S. plants did some Detroit auto executives begin rethinking the narrative of blue-collar failure.
In 1980, an NBC documentary, If Japan Can, Why Cant We, served as a wake-up call for American industry. The documentary introduced the methods of a little-known American quality expert by the name of W. Edwards Deming to an American audience. Deming, the subject of my first book, had helped Japanese companies rebuild following World War II, becoming a hero in Japan. The much-heralded Toyota production system grew out of a years-long dialogue between Deming and the automaker and, via its Kaizen methodology, formalized the way continuous improvement came to encompass Toyotas entire corporate culture and management philosophy.
Responding to an urgent appeal from the new president of Ford, Deming flew to Detroit and, during the next few years, proceeded to rip the lid off of the prevailing assumptions about the quality problems of U.S. companies. It is a testament to how desperate the auto executives were that they grudgingly embraced Demings message, despite the fact that he laid the lions share of the blame for quality problems on senior management instead of on labor.
Fords then-president, Donald E. Petersen, alone among what were then the Big Three top executives, embraced Demings message without reservation. At GM, executives in charge of Cadillac and Pontiac smuggled Deming in via the back door, fearful of how senior management would react. In the coming years, his ideas about a bottom-up, systems-oriented approach to management helped transform both automakers and became associated with, among others, the revival of Cadillac, the Saturn project, and the creation of Fords highly successful Taurus and Sable automobiles.
Deming was a quintessential outsider. Raised in Wyoming, Deming was trained as an engineer and physicist but became a pioneer in statistical sampling methods. At the peak of his popularity, he worked out of the basement of his modest home in Washington, D.C. Driven by a messianic belief in his ideas, Deming would never be as wholeheartedly embraced as his contemporaries were, especially Peter Drucker, who never challenged the fundamental status quo and thus became the darling of twentieth-century CEOs.
At a time when American industry was becoming ever more siloed and finance focused, Deming advocated a collaborative, systems-focused, process-obsessed approach to management. While he was often derided as a mere statistician, Deming made a crucial breakthrough by linking the scientific (in particular, how to understand and manage the statistical variation that erodes the quality of all processes) and the humanistic (an intuitive feel for the organization as a social system and a collaborative, democratic vision of management).
Variation is as ubiquitous as air or water. But a cornerstone of Demings teachings was that only the employees closest to a given process can identify the variation that invariably diminishes quality and develop ideas for improving quality. Ordinary employeesnot senior management or hired consultantsare in the best position to see the cause-and-effect relationships in each process, Deming argued. The challenge for management is to tap into that knowledge on a consistent basis and to make that knowledge actionable. To do so, management must train its employees to identify problems and develop solutions. More controversially, Deming argued, management must also shake up the hierarchy (if not eliminate it entirely), drive fear out of the workplace, and foster intrinsic motivation if it is to make the most of employee potential.
What, readers may be wondering, does industrial improvement in the automotive industry have to do with the ongoing controversy and debates surrounding the quality of American education?
Since the beginning of the millennium, the story of education reform has been, in important respects, a business story. Thats how I, a longtime management writer, first got hooked on the subject. What I aim to demonstrate in the pages that follow is that the corporate-reform industry that is gaining ever-increasing influence on how American schools educate children has largely ignored the successful examples and strategies for improving schools that are hiding in plain sight. These distinct examples together form something of a quiet revolution in education. By casting light on them, this book explores the cultural and organizational infrastructure that schools and districts need in order to achieve lasting improvement. Even as the generative, systems-oriented ideas were finding their way into companies, inspired by Deming and like-minded management thinkers, some schools and school districts around the country were following suit. They were resisting the mandates, the punitive teacher evaluations, and, in some cases, even the standardized tests and were searching forand findingan alternative path.